Home>Knowledge & Skills>Automotive & Repair>How To Build A Roll Cage
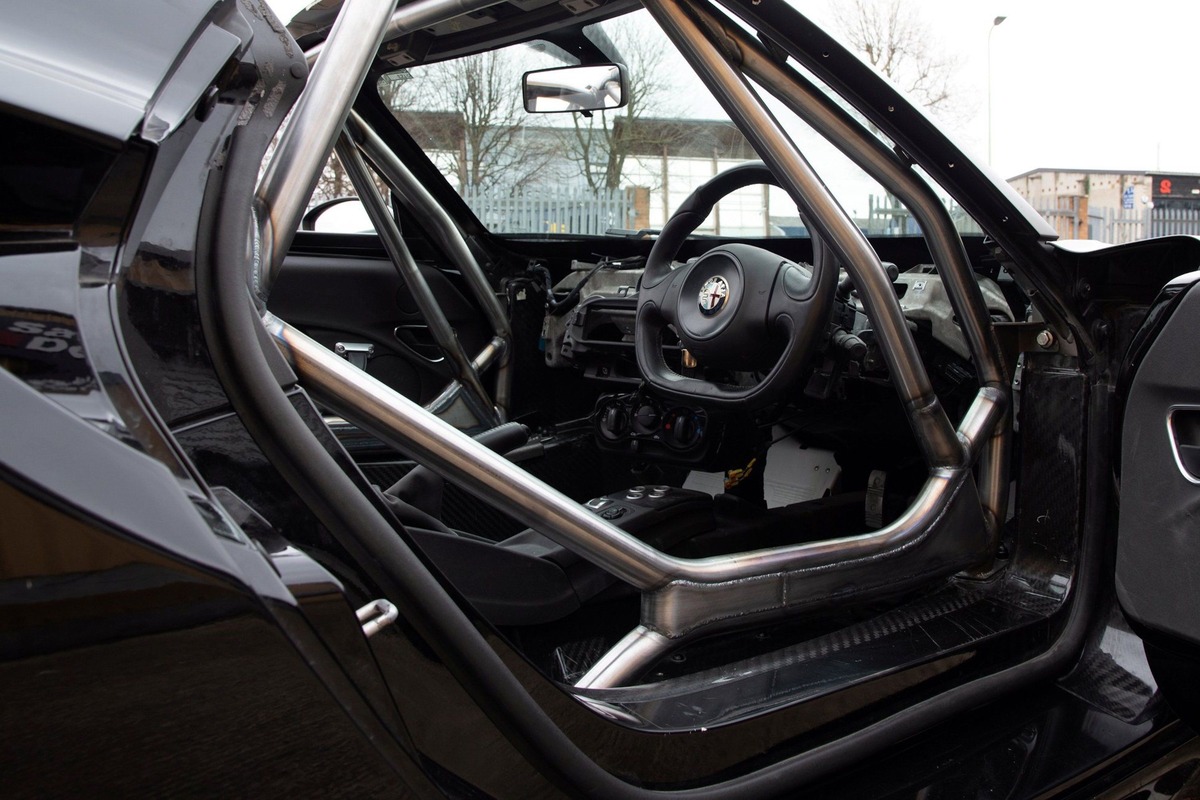
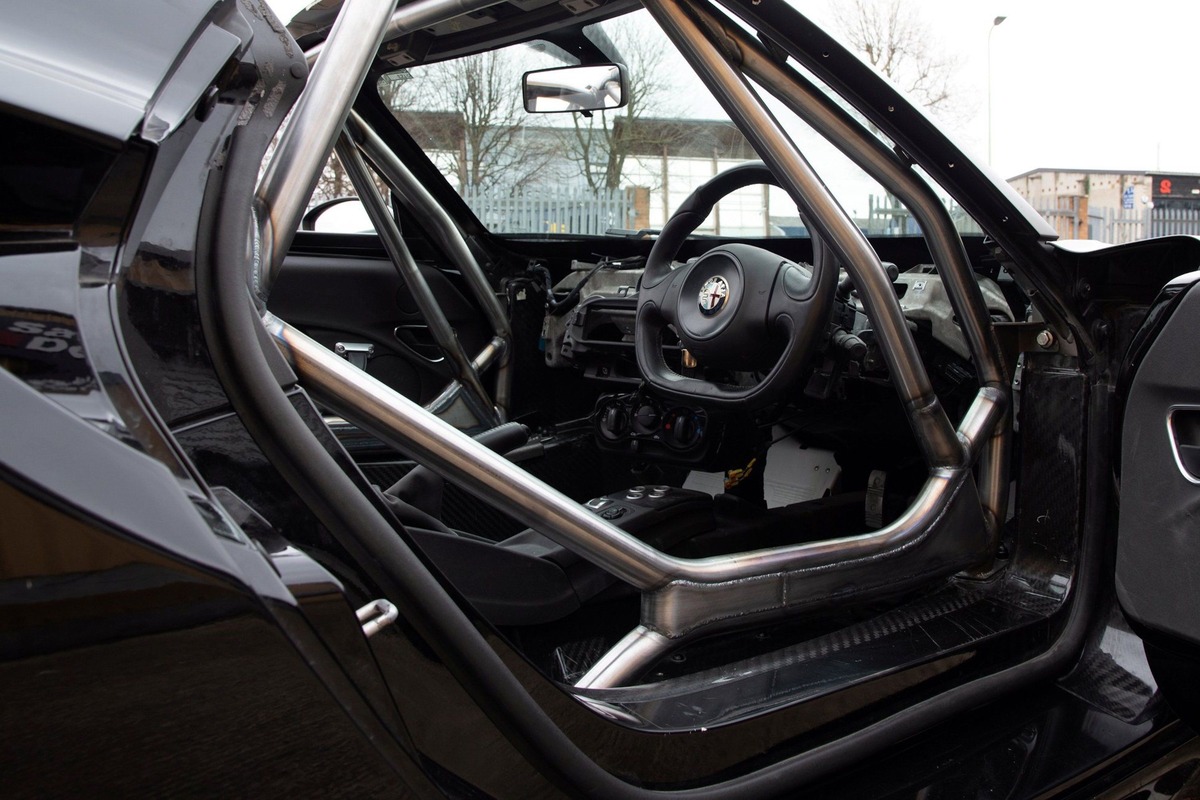
Automotive & Repair
How To Build A Roll Cage
Published: March 7, 2024

Our Editor-in-Chief brings a fresh perspective with his expertise in modern home technologies and eco-friendly solutions. Philip bridges tradition with innovation across a wide range of DIY topics.
Learn how to build a roll cage for automotive repair with our step-by-step guide. Ensure safety and structural integrity with expert tips and techniques.
(Many of the links in this article redirect to a specific reviewed product. Your purchase of these products through affiliate links helps to generate commission for Twigandthistle.com, at no extra cost. Learn more)
Introduction
So, you've got a need for speed and you want to make sure you're safe while tearing up the track or off-roading. Building a roll cage for your vehicle is a crucial step in ensuring your safety in high-performance driving situations. Whether you're a seasoned racer or just a weekend warrior, having a sturdy roll cage can make all the difference in the event of a rollover or collision. In this guide, we'll walk you through the process of building a roll cage for your vehicle, from understanding the basics to the final touches. Let's dive in and get you on the fast track to safety and performance!
Read more: How To Make A Faraday Cage
Understanding Roll Cages
A roll cage is a specially engineered and constructed frame built in or around the passenger compartment of a vehicle to protect its occupants from being injured in an accident, particularly in the event of a rollover. The primary purpose of a roll cage is to provide a protective structure that can prevent the roof from collapsing in the event of a vehicle overturning. Additionally, roll cages also serve to strengthen the chassis of the vehicle, providing rigidity and stability during high-speed maneuvers. They are commonly found in racing cars, off-road vehicles, and even some high-performance street cars.
Key Functions of Roll Cages
- Safety: The foremost function of a roll cage is to protect the occupants of the vehicle in the event of a rollover or collision. It provides a strong and secure structure that can withstand the forces exerted during such incidents, minimizing the risk of injury to the occupants.
- Chassis Reinforcement: Roll cages contribute to the overall structural integrity of the vehicle, enhancing its ability to handle the stresses of high-performance driving. By tying the chassis together, they reduce flex and torsion, improving the handling and stability of the vehicle.
- Mounting Points: Roll cages often serve as mounting points for safety harnesses, seats, and other safety equipment, further enhancing the overall safety of the vehicle.
Types of Roll Cages
- Full Roll Cage: This type of roll cage provides the highest level of protection as it encompasses the entire passenger compartment, including the front and rear sections of the vehicle.
- Roll Bar: A roll bar is a simpler form of a roll cage, typically consisting of a single or multiple bars located behind the driver's seat. While not as comprehensive as a full roll cage, it still provides a significant level of protection, especially in the event of a rear impact or rollover.
Understanding the functions and types of roll cages is essential before embarking on the process of building one for your vehicle. It lays the foundation for designing and constructing a roll cage that meets the specific safety and performance requirements of your driving endeavors.
Designing Your Roll Cage
Designing a roll cage is a critical step that requires careful planning and consideration of various factors to ensure its effectiveness and compliance with safety standards. Here are the key aspects to focus on when designing your roll cage:
Vehicle-Specific Considerations
When designing a roll cage, it's essential to take into account the specific make and model of the vehicle. Different vehicles have varying structural characteristics and dimensions, which can significantly impact the design and installation of a roll cage. Consider the vehicle's body style, interior space, and any modifications that may affect the placement and configuration of the roll cage.
Safety Regulations and Standards
Familiarize yourself with the safety regulations and standards that apply to roll cage construction, particularly if you intend to use the vehicle for competitive racing or off-road events. Organizations such as the National Hot Rod Association (NHRA) and the Federation Internationale de l'Automobile (FIA) have specific guidelines for roll cage design and installation. Ensure that your design complies with these regulations to guarantee its legality and effectiveness.
Structural Integrity and Load Distribution
The design of a roll cage should prioritize structural integrity and load distribution to effectively withstand the forces experienced during a rollover or collision. Consider the placement of main structural members, such as the main hoop, front and rear braces, and door bars, to create a robust framework that evenly distributes impact forces throughout the vehicle's chassis.
Occupant Position and Accessibility
Take into consideration the positioning of the vehicle's occupants when designing the roll cage. Ensure that the roll cage does not obstruct entry and exit from the vehicle and provides adequate headroom and clearance for the occupants. Additionally, consider the installation of door bars and crossbars to enhance occupant protection without compromising accessibility.
Read more: How to Build a DIY Roll Up Door
Customization and Additional Features
Depending on the intended use of the vehicle, you may need to customize the roll cage design to accommodate specific safety equipment, such as racing harnesses, seats, and fire suppression systems. Incorporating mounting points and provisions for additional safety features during the design phase can streamline the installation process and ensure seamless integration with the roll cage structure.
By carefully considering these aspects during the design phase, you can create a roll cage that not only meets safety requirements but also aligns with the specific needs and characteristics of your vehicle. A well-designed roll cage forms the foundation for a safer and more resilient vehicle, providing peace of mind during high-performance driving scenarios.
Choosing the Right Materials
Selecting the appropriate materials for constructing a roll cage is paramount to ensuring its strength, durability, and overall effectiveness in safeguarding vehicle occupants. The following factors should be considered when choosing the materials for your roll cage:
Material Selection Criteria
-
Steel Alloys: High-strength steel alloys, such as chromoly steel (chromium-molybdenum), are commonly used in roll cage construction due to their exceptional strength-to-weight ratio. These alloys offer superior tensile and yield strength, making them ideal for withstanding the forces exerted during impact or rollover events.
-
Aluminum Alloys: While less commonly used than steel, aluminum alloys can be employed in roll cage construction, particularly in applications where weight reduction is a priority. Aluminum offers a favorable strength-to-weight ratio and can contribute to reducing the overall weight of the vehicle, enhancing its performance characteristics.
-
Tubing Specifications: The selection of tubing specifications, including outer diameter, wall thickness, and material grade, plays a crucial role in determining the structural integrity of the roll cage. Thicker-walled tubing with larger diameters provides increased resistance to deformation and bending, enhancing the protective capabilities of the roll cage.
-
Certification Compliance: When choosing materials for a roll cage intended for competitive racing or sanctioned events, it is essential to ensure that the selected materials comply with the safety standards and certifications mandated by relevant governing bodies. Certain organizations specify approved materials and tubing specifications to ensure uniform safety across participating vehicles.
Considerations for Material Compatibility
-
Weldability: The selected materials should exhibit favorable weldability characteristics to facilitate the fabrication and assembly of the roll cage structure. Ensuring compatibility with common welding processes, such as TIG (Tungsten Inert Gas) or MIG (Metal Inert Gas) welding, is essential for achieving strong and reliable weld joints.
-
Corrosion Resistance: In applications where the vehicle is exposed to moisture, corrosive elements, or environmental factors, choosing materials with inherent corrosion resistance, or implementing protective coatings, can prolong the service life of the roll cage and maintain its structural integrity over time.
-
Weight Considerations: Balancing the strength and weight of the materials is crucial, especially in performance-oriented vehicles. Lightweight materials can contribute to improved handling and agility, while still providing the necessary protection, whereas excessively heavy materials may compromise the vehicle's performance characteristics.
-
Material Compatibility with Attachments: Consider the compatibility of the chosen materials with attachment methods for additional safety equipment, such as seat mounts, harness anchors, and roll cage padding. Ensuring that the materials allow for secure and reliable attachment of safety components is essential for comprehensive occupant protection.
By carefully evaluating these criteria and considerations, you can make informed decisions when selecting the materials for your roll cage, ultimately contributing to the creation of a robust and reliable safety structure for your vehicle.
Tools and Equipment Needed
When embarking on the construction of a roll cage, having the right tools and equipment at your disposal is essential to ensure the precision and quality of the fabrication process. Here's a comprehensive list of the tools and equipment needed to undertake the construction of a roll cage:
Measuring and Marking Tools
- Tape Measure: Essential for accurately measuring tubing lengths and dimensions.
- Marker or Soapstone: Used for marking cut lines and reference points on the tubing.
Cutting and Shaping Tools
- Tube Notcher: Facilitates the precise notching of tubing for seamless joints and fitment.
- Angle Grinder with Cutting Disc: Enables the cutting of tubing to the required lengths and angles.
- Band Saw or Chop Saw: Provides an alternative method for cutting tubing with precision.
Welding Equipment
- Welder (TIG or MIG): Utilized for welding the tubing joints and structural components.
- Welding Clamps and Magnets: Aid in securing tubing in position during the welding process.
- Grinding and Deburring Tools: Essential for smoothing and cleaning welded joints for a professional finish.
Fabrication Tools
- Bender (Manual or Hydraulic): Required for bending tubing to the desired angles and radii.
- Hole Saw or Punch: Used for creating holes in the tubing for mounting points and connections.
- Vise and Workbench: Provides a stable platform for assembly and fabrication tasks.
Safety Equipment
- Welding Helmet and Gloves: Essential for protecting the eyes and hands during welding operations.
- Safety Glasses and Respirator: Ensures personal safety when cutting, grinding, and welding.
Additional Supplies
- Tubing and Material Stock: The primary raw materials for constructing the roll cage.
- Welding Consumables: Including filler rod, welding wire, and shielding gas (if applicable).
- Protective Coverings and Fire Extinguisher: Precautionary measures for fire safety during welding.
Having access to these tools and equipment is fundamental to the successful fabrication of a roll cage. Prioritize safety and precision throughout the construction process, and ensure that all tools and equipment are in good working condition before commencing the project.
Building the Main Structure
The construction of the main structure of a roll cage forms the core of the fabrication process, laying the foundation for the overall safety and integrity of the vehicle. This phase involves the assembly and welding of the primary structural components that define the protective framework of the roll cage. Here's a detailed breakdown of the steps involved in building the main structure:
Read more: How to Build a Kitchen Island Extension
1. Preparing the Tubing
Before commencing the assembly, it's essential to prepare the tubing by cutting it to the required lengths and notching the ends to facilitate seamless joints. Accurate measurements and precise cutting are crucial to ensure the proper fitment and alignment of the tubing during assembly.
2. Positioning the Main Hoop
The main hoop, which forms the central backbone of the roll cage, is positioned and secured within the vehicle's interior. Careful consideration should be given to its placement to ensure adequate clearance and structural integration with the vehicle's chassis.
3. Attaching Front and Rear Braces
Front and rear braces are then attached to the main hoop, extending towards the vehicle's front and rear sections. These braces play a pivotal role in distributing impact forces and reinforcing the overall structure of the roll cage.
4. Installing Door Bars
Door bars are integrated into the main structure to provide lateral protection and enhance the rigidity of the roll cage. Their positioning should account for occupant accessibility and safety without compromising structural integrity.
Read more: How to Build a DIY Garage Foundation
5. Cross-Bracing and Diagonal Supports
Cross-bracing and diagonal supports are added to the main structure to further enhance its resistance to torsional forces and lateral impacts. These components contribute to the overall stability and load distribution of the roll cage.
6. Test-Fitting and Alignment
Throughout the assembly process, test-fitting and alignment checks are conducted to ensure that all components fit together seamlessly and align with the vehicle's interior contours. This iterative process is essential for achieving a precise and secure fit.
7. Welding and Reinforcement
Once the components are properly positioned and aligned, welding is performed to create strong and durable joints. Reinforcement plates and gussets may be added at critical junctions to enhance the structural integrity of the weld joints.
8. Quality Assurance and Inspection
After the main structure is welded, a thorough inspection is carried out to verify the quality of the welds, the alignment of components, and the overall integrity of the roll cage. Any necessary adjustments or reinforcements are made to address any discrepancies.
By meticulously following these steps, the main structure of the roll cage is constructed with precision and attention to detail, ensuring that it provides the necessary protection and reinforcement for the vehicle's occupants. This phase sets the stage for the subsequent installation of additional support components and the completion of the roll cage assembly.
Read more: How to Build DIY Wall Panels
Installing Additional Support
Once the main structure of the roll cage is in place, the installation of additional support components further enhances its strength and resilience. These supplementary elements play a crucial role in fortifying the roll cage and ensuring comprehensive protection for the vehicle occupants. Here's a detailed overview of the process for installing additional support:
1. Harness Bars and Mounting Points
Harness bars, also known as harness crossbars, are integrated into the roll cage to serve as mounting points for racing harnesses. These bars are strategically positioned to accommodate the secure attachment of safety harnesses, ensuring that they effectively restrain the occupants in the event of a collision or rollover. Proper placement and reinforcement of harness mounting points are essential to withstand the forces exerted during sudden deceleration or impact.
2. Diagonal and X-Braces
Diagonal and X-braces are added to the roll cage structure to further reinforce its resistance to torsional forces and lateral impacts. These braces create a network of interconnected support, effectively distributing the energy from impacts throughout the roll cage. By strategically positioning and welding these braces, the overall rigidity and load-bearing capacity of the roll cage are significantly enhanced.
3. Roof and A-Pillar Supports
In certain roll cage designs, roof and A-pillar supports are incorporated to provide additional reinforcement to the upper structure of the vehicle. These supports help prevent roof collapse in the event of a rollover and contribute to maintaining the integrity of the vehicle's passenger compartment. Careful consideration is given to the attachment points and welding of these supports to ensure optimal strength and stability.
Read more: DIY: How to Build a Door
4. Gusset Plates and Reinforcements
Gusset plates and reinforcements are strategically added at critical junctions and stress points within the roll cage structure. These components serve to strengthen the weld joints and mitigate potential points of weakness. By distributing the stress and load across a wider area, gusset plates and reinforcements contribute to the overall durability and resilience of the roll cage.
5. Padding and Coverings
To enhance occupant safety and comfort, padding and coverings may be installed on certain sections of the roll cage. These additions help mitigate the risk of injury in the event of incidental contact with the roll cage during driving maneuvers. Additionally, padding can reduce the transmission of noise and vibrations into the vehicle's interior, improving the overall driving experience.
By meticulously installing these additional support components, the roll cage is fortified to withstand a wide range of dynamic forces and potential impacts. The comprehensive reinforcement provided by these elements ensures that the roll cage effectively fulfills its critical role in protecting the vehicle occupants during high-performance driving scenarios.
Welding and Finishing Touches
After the main structure and additional support components are in place, the welding and finishing touches phase is crucial to ensure the structural integrity and professional appearance of the roll cage. This phase involves meticulous welding of joints, as well as the implementation of finishing details to enhance the overall functionality and aesthetics of the roll cage.
1. Welding Process
The welding of the roll cage components demands precision and expertise to create strong and reliable joints. TIG (Tungsten Inert Gas) or MIG (Metal Inert Gas) welding processes are commonly employed for roll cage fabrication, offering the necessary control and penetration to achieve high-quality welds. Welding is performed in accordance with established welding procedures, ensuring proper heat input and fusion to create durable connections between the tubing and structural elements.
Read more: How to Build a DIY Pocket Door
2. Seam Welding and Reinforcement
Seam welding, where continuous welds are applied along critical joints and connections, is employed to enhance the strength and load-bearing capacity of the roll cage. Additionally, reinforcement plates and gussets are strategically welded at key stress points to fortify the structure and mitigate potential areas of weakness. These reinforcements contribute to the overall resilience of the roll cage, particularly in high-stress scenarios.
3. Grinding and Smoothing
Following the welding process, the welded joints and seams are carefully ground and smoothed to achieve a clean and professional finish. This step involves the use of grinding tools to remove excess weld material and create smooth transitions between the tubing and welded components. Smoothing the welds not only improves the aesthetic appeal of the roll cage but also eliminates potential points of abrasion for the occupants.
4. Surface Treatment and Coatings
To protect the roll cage from corrosion and environmental elements, surface treatment and coatings may be applied to the welded areas. This can include the application of corrosion-resistant coatings or paints to safeguard the roll cage against rust and deterioration. Additionally, heat-affected zones resulting from welding may be treated to restore the material's original properties and mitigate potential weaknesses.
5. Final Inspection and Quality Assurance
Upon completing the welding and finishing touches, a comprehensive inspection is conducted to verify the quality of the welds, the integrity of the structure, and the overall compliance with safety standards. Any imperfections or deficiencies are addressed, and necessary adjustments are made to ensure that the roll cage meets the required specifications and performance criteria.
By meticulously executing the welding process and attending to the finishing details, the roll cage is not only structurally robust but also presents a professional and refined appearance. This phase marks the culmination of the fabrication process, setting the stage for the final testing and certification of the roll cage before it is put into service.
Read more: How to Build a Butcher Block Island
Testing and Certification
The testing and certification phase is a critical step in validating the structural integrity and safety compliance of the constructed roll cage. This phase involves a series of assessments and evaluations to ensure that the roll cage meets the requisite standards and regulations for its intended use. Here's a comprehensive overview of the testing and certification process:
1. Dimensional and Fitment Checks
Before subjecting the roll cage to formal testing, dimensional and fitment checks are conducted to verify its alignment and compatibility with the vehicle's interior. This involves assessing the clearances, positioning of mounting points, and overall integration of the roll cage within the vehicle's structure. Any discrepancies or deviations from the intended design are addressed to ensure proper fitment.
2. Load and Stress Testing
The roll cage undergoes load and stress testing to assess its capacity to withstand dynamic forces and impacts. This testing involves subjecting the roll cage to simulated loads and stresses representative of high-performance driving scenarios, such as sudden deceleration, lateral impacts, and vertical forces. The roll cage's ability to resist deformation and maintain its protective function is thoroughly evaluated.
3. Material and Weld Quality Inspection
A detailed inspection of the roll cage's materials and weld quality is conducted to assess the integrity of the fabrication. This includes non-destructive testing methods, such as visual inspection, dye penetrant testing, and ultrasonic testing, to identify potential defects, discontinuities, or imperfections in the materials and weld joints. The aim is to ensure that the roll cage's construction meets the specified material and welding standards.
Read more: How to Build a DIY Camper Door
4. Compliance with Safety Regulations
The roll cage is evaluated for compliance with safety regulations and standards set forth by relevant governing bodies, such as motorsport associations and regulatory agencies. This assessment ensures that the roll cage meets the prescribed guidelines for structural design, material specifications, and installation requirements. Any non-compliance issues are addressed to align the roll cage with the applicable safety regulations.
5. Dynamic Vehicle Testing
In certain cases, the roll cage may undergo dynamic vehicle testing to evaluate its performance under real-world driving conditions. This involves installing the roll cage in a representative vehicle and conducting on-track or off-road testing to assess its behavior during high-speed maneuvers, cornering, and simulated collision scenarios. The roll cage's impact on vehicle dynamics and occupant safety is thoroughly scrutinized.
6. Certification and Documentation
Upon successful completion of the testing and evaluation process, the roll cage is certified as compliant with the requisite safety standards. Documentation detailing the testing procedures, results, and certification status is prepared to provide a comprehensive record of the roll cage's compliance. This documentation serves as a validation of the roll cage's safety and structural integrity for regulatory and competitive purposes.
By subjecting the roll cage to rigorous testing and certification procedures, its suitability for high-performance driving applications is confirmed, providing assurance of occupant safety and regulatory compliance. This phase marks the culmination of the roll cage construction process, ensuring that the fabricated structure meets the highest safety standards and performance criteria.
Conclusion
In conclusion, building a roll cage for your vehicle is a significant undertaking that demands meticulous planning, precise fabrication, and adherence to safety standards. The construction of a roll cage not only enhances the safety of the vehicle's occupants during high-performance driving but also contributes to the overall structural integrity and chassis reinforcement. By understanding the fundamental principles of roll cage design, selecting the appropriate materials, and executing the fabrication process with precision, you can create a robust and reliable safety structure for your vehicle.
The comprehensive approach to roll cage construction, encompassing the design, material selection, fabrication, and testing phases, ensures that the resulting roll cage meets the stringent requirements for safety and performance. Whether it's for competitive racing, off-road adventures, or enhanced on-road safety, a well-built roll cage provides peace of mind and protection in dynamic driving scenarios.
By following the guidelines outlined in this comprehensive guide, you can embark on the journey of constructing a roll cage with confidence, knowing that you are prioritizing the safety and resilience of your vehicle. The careful consideration of design elements, the meticulous execution of fabrication techniques, and the rigorous testing and certification process collectively contribute to the creation of a roll cage that not only meets but exceeds the expectations for safety and performance.
Ultimately, the construction of a roll cage is a testament to the commitment to safety and the pursuit of excellence in high-performance driving. It represents a critical investment in the protection of both the vehicle and its occupants, ensuring that they are equipped to handle the demands of dynamic driving environments with confidence and security.