Home>Create & Decorate>DIY & Crafts>DIY Air Compressor: Step-by-Step Guide To Building Your Own
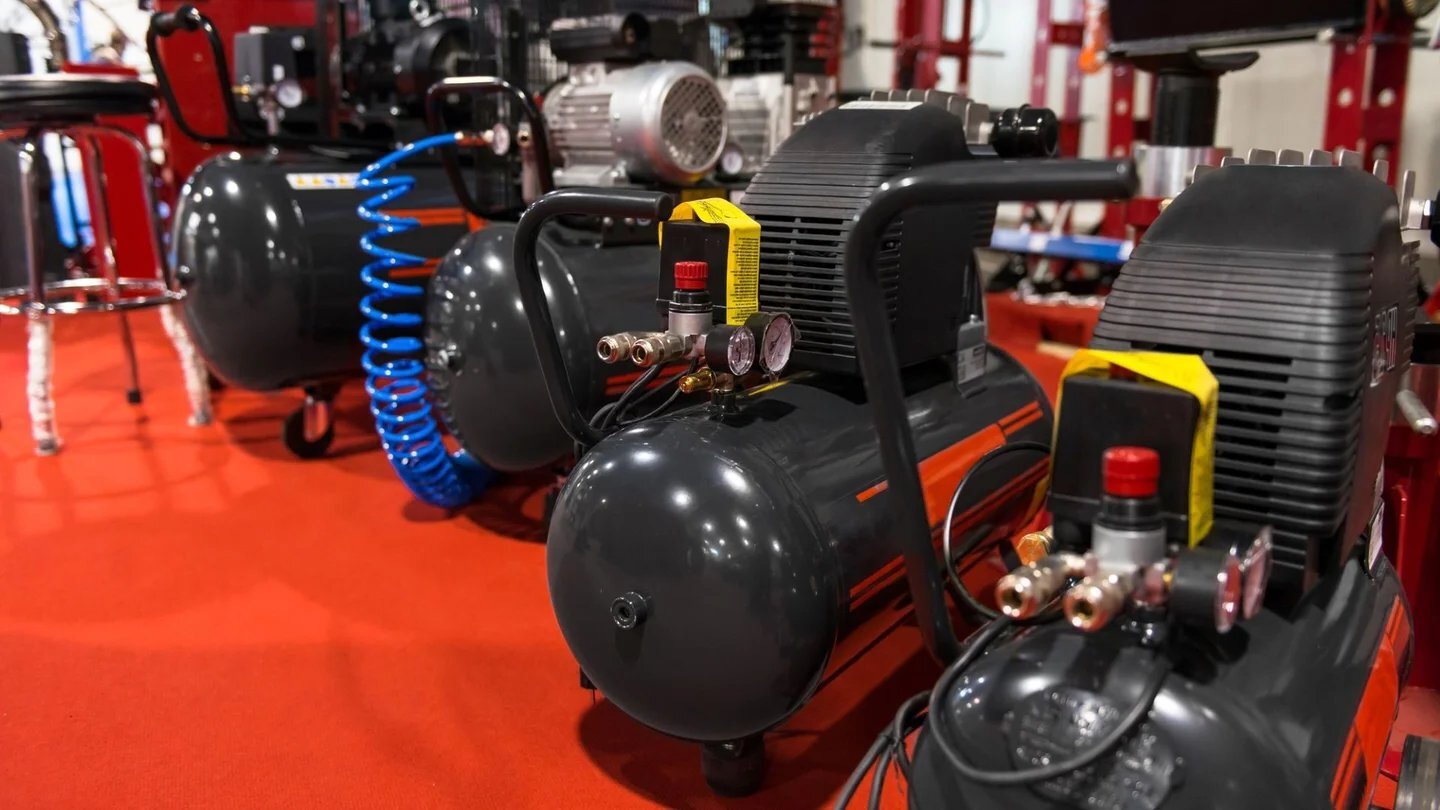
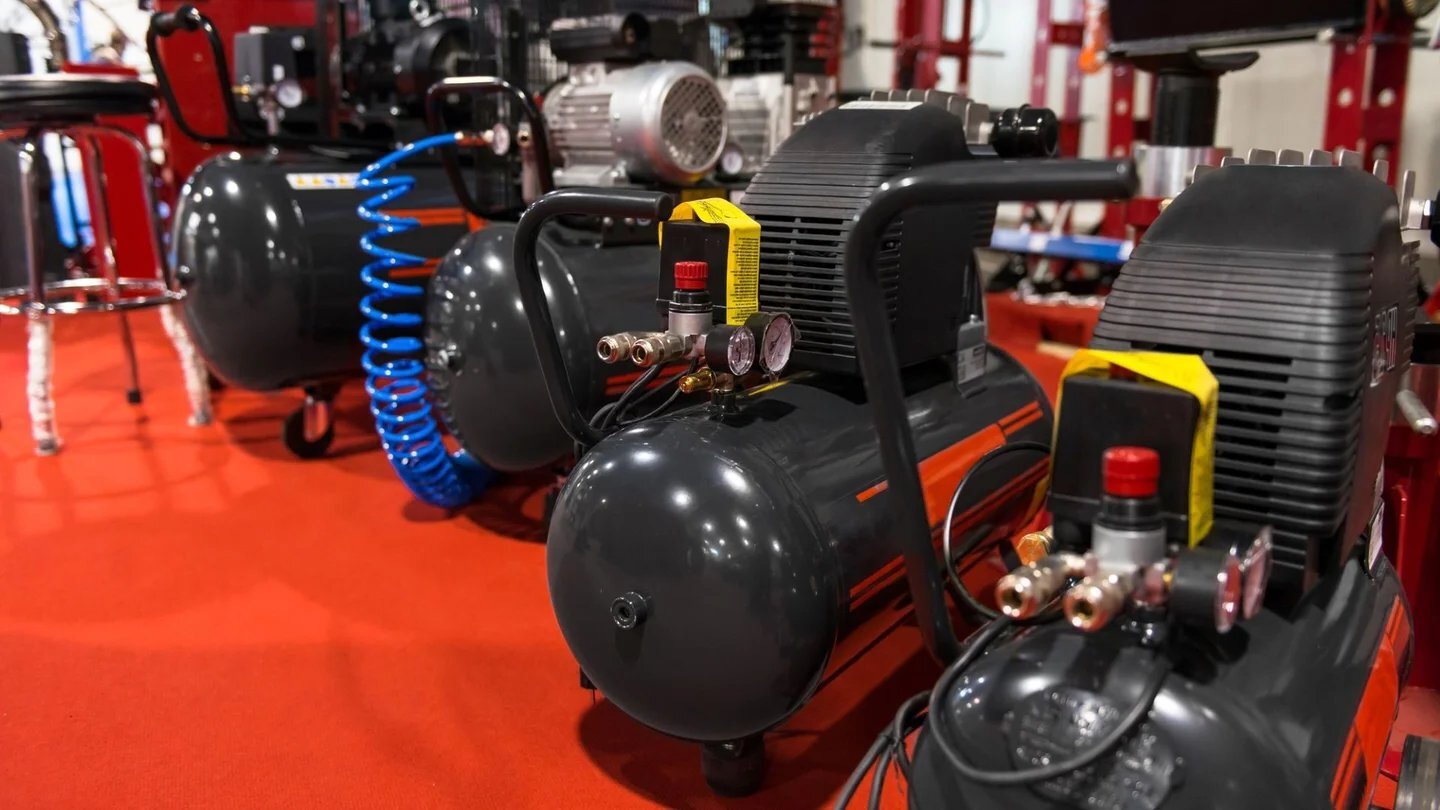
DIY & Crafts
DIY Air Compressor: Step-by-Step Guide To Building Your Own
Published: June 5, 2024

Senior Editor in Create & Decorate, Kathryn combines traditional craftsmanship with contemporary trends. Her background in textile design and commitment to sustainable crafts inspire both content and community.
Learn how to build your own air compressor with our step-by-step DIY guide. Perfect for DIY & Crafts enthusiasts looking for a new project.
(Many of the links in this article redirect to a specific reviewed product. Your purchase of these products through affiliate links helps to generate commission for Twigandthistle.com, at no extra cost. Learn more)
Introduction
Are you tired of spending a fortune on air compressors for your DIY projects? Why not take matters into your own hands and build your own DIY air compressor? Not only will this save you money, but it will also give you the satisfaction of creating something useful with your own two hands. In this step-by-step guide, we will walk you through the process of building your very own air compressor, from understanding the basics to gathering the necessary materials and tools, to the final testing and troubleshooting. So, roll up your sleeves and get ready to dive into the world of DIY air compressors!
Read more: How to DIY Window Seal for Portable AC
Understanding the Basics of Air Compressors
Before diving into the construction of your DIY air compressor, it's essential to grasp the fundamental principles of how air compressors work. An air compressor is a device that converts power, typically from an electric motor, diesel, or gasoline engine, into potential energy stored in pressurized air. This compressed air can then be used for various applications, such as powering pneumatic tools, inflating tires, or even operating HVAC control systems. The key components of an air compressor include the air tank, compressor pump, motor, pressure switch, regulator, and safety valve. Understanding how these components work together will lay the groundwork for successfully building your own DIY air compressor.
Key Concepts to Understand:
- Compression Process: Air compressors work by drawing in air and compressing it to increase its pressure. This is typically achieved through a piston-cylinder arrangement or a rotating impeller.
- Tank Capacity: The size of the air tank determines the amount of compressed air that can be stored. Larger tanks can provide a more consistent airflow for longer durations.
- Compressor Pump Types: There are various types of compressor pumps, including reciprocating, rotary screw, and centrifugal. Each type has its own advantages and is suitable for different applications.
- Pressure Regulation: A pressure switch and regulator are crucial for controlling the output pressure of the compressor, ensuring it matches the requirements of the intended applications.
- Safety Considerations: Understanding the importance of safety features such as pressure relief valves and automatic cut-off systems is vital to prevent over-pressurization and potential hazards.
By familiarizing yourself with these basic concepts, you'll be better equipped to proceed with the construction of your DIY air compressor.
Gathering the Necessary Materials and Tools
Before you embark on the journey of building your DIY air compressor, it's crucial to gather all the necessary materials and tools. Having everything at your fingertips will streamline the construction process and minimize any potential delays. Here's a comprehensive list of the items you'll need to get started:
Materials:
- Air Tank: Look for a sturdy air tank with the capacity that suits your intended applications. You can repurpose an old air tank or purchase a new one from a hardware store.
- Compressor Pump: Select a compressor pump that matches the airflow and pressure requirements of your projects. Consider factors such as pump type, horsepower, and duty cycle.
- Motor: Depending on the power source you prefer, choose an electric motor, gasoline engine, or diesel engine that aligns with the specifications of your compressor pump.
- Pressure Switch and Regulator: These components are essential for controlling the output pressure of the air compressor. Ensure they are compatible with your chosen compressor pump.
- Safety Valve: A safety valve is a critical safety feature that releases air if the pressure in the tank exceeds the maximum level. It's a non-negotiable component for your DIY air compressor.
- Fittings and Tubing: Gather a variety of fittings, connectors, and tubing to facilitate the airflow between the components of your air compressor.
- Mounting Hardware: Depending on your design, you may need bolts, nuts, and brackets to securely mount the components onto the air tank or a base.
Read more: How to Build a DIY Magnetic Screen Door
Tools:
- Wrenches and Sockets: A set of wrenches and sockets will be indispensable for assembling and tightening the various components of the air compressor.
- Drill and Bits: You'll need a drill and a selection of drill bits to create mounting holes and install fittings on the air tank.
- Welding Equipment: If you plan to fabricate custom brackets or modify the air tank, welding equipment such as a welder and safety gear will be necessary.
- Cutting Tools: Depending on the materials you're working with, cutting tools such as a hacksaw, reciprocating saw, or angle grinder may be required.
- Measuring Instruments: Accurate measurements are crucial in the construction process. Have a tape measure, square, and level on hand.
- Safety Gear: Prioritize safety by wearing protective gear, including gloves, safety glasses, and ear protection, especially when working with power tools and compressed air.
By ensuring you have all the required materials and tools ready, you'll be well-prepared to move on to the next phase of building your DIY air compressor.
Step 1: Building the Air Tank
Building the air tank is the foundational step in constructing your DIY air compressor. The air tank serves as the reservoir for storing the compressed air before it is utilized for various applications. Here's a detailed guide on how to build the air tank for your DIY air compressor:
1. Selecting the Air Tank:
- Choose a suitable air tank based on the airflow and pressure requirements of your projects. Ensure the tank is rated for the maximum pressure that your compressor pump can deliver.
- If you're repurposing an old air tank, thoroughly inspect it for any signs of corrosion, damage, or weakened spots. Safety should always be a top priority when working with pressurized vessels.
2. Mounting the Components:
- Position the compressor pump, motor, pressure switch, regulator, and safety valve on the air tank or a sturdy base. Ensure they are securely mounted and aligned for efficient airflow and operation.
- Use appropriate mounting hardware such as bolts, nuts, and brackets to affix the components in place. Consider the weight and vibration of the components when selecting the mounting hardware.
Read more: How to DIY Duct a Window Air Conditioner
3. Installing Fittings and Connectors:
- Drill and tap the necessary holes in the air tank for installing fittings, connectors, and valves. Use thread sealant or Teflon tape to ensure airtight connections and prevent leaks.
- Connect the outlet of the compressor pump to the inlet of the air tank using suitable tubing and fittings. Similarly, connect the pressure switch, safety valve, and regulator to their respective ports on the air tank.
4. Pressure Testing:
- Before proceeding further, conduct a pressure test to ensure the integrity of the air tank and the connections. Gradually pressurize the tank to the maximum working pressure and check for any leaks or abnormal pressure drops.
- It's crucial to perform this test in a safe environment and follow all recommended safety precautions. Any signs of weakness or leaks should be addressed before proceeding with the next steps.
By following these steps, you'll successfully build the air tank for your DIY air compressor, laying the groundwork for the subsequent installation of the compressor pump and other essential components. Remember to prioritize safety at every stage of the construction process to ensure the reliable and safe operation of your DIY air compressor.
Step 2: Installing the Compressor Pump
Once the air tank is securely in place, the next crucial step in building your DIY air compressor is installing the compressor pump. The compressor pump is responsible for drawing in air and compressing it to the desired pressure, which is then stored in the air tank for future use. Here's a detailed guide on how to install the compressor pump:
-
Positioning the Compressor Pump:
- Place the compressor pump in a location that allows for efficient airflow and easy access for maintenance. Ensure that it is aligned with the mounting holes on the air tank or base.
-
Securing the Pump in Place:
- Use appropriate mounting hardware, such as bolts, washers, and nuts, to securely fasten the compressor pump to the designated mounting points. Consider the weight and vibration of the pump when selecting the mounting hardware.
-
Aligning the Components:
- Align the pulley or drive system of the compressor pump with the motor's pulley or drive shaft. This alignment is crucial for the efficient transfer of power from the motor to the pump.
-
Connecting the Motor to the Pump:
- If using an electric motor, connect the motor to the compressor pump using a suitable belt or direct drive coupling. Ensure that the connection is secure and properly tensioned to facilitate smooth power transmission.
-
Checking the Pump's Oil Level:
- If the compressor pump requires lubrication, check and fill the pump's oil reservoir to the recommended level. Refer to the manufacturer's guidelines for the specific type of oil and the correct filling procedure.
-
Electrical Connections (If Applicable):
- If the compressor pump is powered by an electric motor, make the necessary electrical connections following the motor manufacturer's wiring diagram. Ensure that all electrical connections are properly insulated and secured to prevent any electrical hazards.
-
Testing the Pump Operation:
- Before proceeding further, conduct a brief test run of the compressor pump to ensure that it operates smoothly and without any unusual noises or vibrations. This initial test will help identify any potential issues that need to be addressed before proceeding.
By following these steps, you'll successfully install the compressor pump, a critical component of your DIY air compressor. Once the pump is in place and operational, you can proceed to the next phase of connecting the various components and conducting the final testing and troubleshooting to ensure the functionality and safety of your DIY air compressor.
Step 3: Connecting the Components
Connecting the components of your DIY air compressor is a pivotal step that brings together the various elements to create a functional and efficient system. Proper connections ensure seamless airflow, pressure regulation, and safety features. Here's a detailed guide on how to connect the components of your DIY air compressor:
-
Airflow Pathway:
- Establish a clear airflow pathway from the compressor pump to the air tank and from the tank to the outlet. Use high-quality tubing and fittings to minimize air leaks and pressure drops.
- Ensure that the tubing is securely connected to the compressor pump's outlet and the air tank's inlet. Use appropriate fittings and thread sealant to create airtight connections.
-
Pressure Regulation:
- Connect the pressure switch to the compressor pump and the air tank. The pressure switch is responsible for monitoring the air tank's pressure and controlling the compressor pump's operation to maintain the desired pressure level.
- Install a regulator downstream of the air tank to allow for precise adjustment of the output pressure. Connect the regulator to the air tank and the outlet for pneumatic tools or other applications.
-
Safety Features:
- Connect the safety valve to the air tank to provide over-pressure protection. The safety valve will release air if the pressure in the tank exceeds the preset limit, preventing potential hazards.
- Ensure that the safety valve is oriented in a direction that directs the released air away from any personnel or sensitive equipment.
-
Electrical Connections:
- If your DIY air compressor is powered by an electric motor, make the necessary electrical connections following the motor manufacturer's wiring diagram. Ensure that all connections are properly insulated and secured to prevent electrical hazards.
-
Testing the Connections:
- After making the connections, conduct a thorough inspection of all fittings, tubing, and electrical connections to ensure they are secure and properly aligned.
- Perform a brief test run of the air compressor to verify that the airflow is consistent, the pressure regulation functions as intended, and the safety features operate correctly.
By meticulously connecting the components of your DIY air compressor, you'll create a reliable and safe system that is ready for the final phase of testing and troubleshooting. Pay close attention to the details of each connection to ensure optimal performance and safety.
Read more: How to Make DIY Window Screens
Step 4: Adding Safety Features
Safety should always be a top priority when building any DIY equipment, and an air compressor is no exception. Adding essential safety features to your DIY air compressor is crucial to prevent potential hazards and ensure the reliable and secure operation of the system. Here's a detailed guide on how to incorporate safety features into your DIY air compressor:
-
Safety Valve Installation:
- Install a safety valve on the air tank to provide over-pressure protection. The safety valve serves as a critical fail-safe mechanism that releases air if the pressure in the tank exceeds the preset limit. This prevents the tank from reaching dangerously high pressures, reducing the risk of ruptures or explosions.
-
Pressure Relief System:
- Consider incorporating a pressure relief system that automatically releases excess pressure from the air tank. This additional safety measure further mitigates the risk of over-pressurization, especially in the event of a malfunction or system failure.
-
Automatic Cut-Off System:
- Implement an automatic cut-off system that shuts down the compressor pump when the pressure in the air tank reaches the maximum allowable level. This feature prevents the system from continuing to operate under unsafe conditions, offering an additional layer of protection.
-
Safety Signage and Instructions:
- Clearly label the air compressor with safety instructions and warnings to alert users about potential risks and proper operating procedures. This includes indicating the location of the safety valve, emergency shut-off procedures, and any specific precautions for safe usage.
-
Air Tank Inspection:
- Regularly inspect the air tank for signs of corrosion, damage, or weakening. Any compromised areas should be addressed immediately to maintain the structural integrity of the tank and prevent potential safety hazards.
-
Safety Gear and Training:
- Provide appropriate safety gear, such as eye protection, hearing protection, and gloves, for anyone operating or working near the DIY air compressor. Additionally, ensure that users are adequately trained in the safe operation and maintenance of the equipment.
By incorporating these safety features into your DIY air compressor, you'll create a system that prioritizes the well-being of its users and minimizes the risk of accidents or equipment failures. Remember, safety is not just an option – it's a fundamental requirement for any DIY project, especially when it involves the construction of potentially hazardous equipment like an air compressor.
Step 5: Testing and Troubleshooting
Once you have assembled your DIY air compressor, it's crucial to conduct thorough testing and troubleshooting to ensure its functionality and safety. Here's a detailed guide on how to approach the testing and troubleshooting phase:
-
Initial Inspection:
- Before testing the air compressor, perform a visual inspection of all components, connections, and safety features. Look for any signs of leaks, loose fittings, or potential hazards. Address any issues discovered during the inspection.
-
Pressure Test:
- Gradually pressurize the air tank to the maximum working pressure and monitor it for any abnormal pressure drops or leaks. Use a pressure gauge to verify that the pressure switch and safety valve operate as intended.
-
Functional Testing:
- Test the compressor pump's operation by running it without load and ensuring that it builds up pressure in the air tank as expected. Listen for any unusual noises or vibrations that may indicate mechanical issues.
-
Airflow and Regulation:
- Verify that the airflow from the air tank to the outlet is consistent and regulated by the pressure switch and regulator. Test the regulator's adjustment to confirm that it can control the output pressure effectively.
-
Electrical System Check:
- If the air compressor is powered by an electric motor, check the electrical connections, motor operation, and the functionality of the pressure switch in controlling the motor's activation and deactivation.
-
Safety Feature Testing:
- Trigger the safety valve manually to ensure that it releases air when the pressure exceeds the set limit. Test the automatic cut-off system by simulating a pressure build-up and verifying that the compressor pump shuts down at the designated pressure level.
-
Troubleshooting:
- If any issues are identified during the testing phase, systematically troubleshoot each component and connection to pinpoint the root cause. Common issues may include air leaks, pressure irregularities, or electrical malfunctions.
-
Addressing Identified Issues:
- Once the issues are identified, take the necessary steps to address them. This may involve tightening fittings, replacing faulty components, adjusting pressure settings, or revisiting the electrical connections.
-
Re-Testing:
- After addressing the identified issues, re-test the air compressor to ensure that the problems have been resolved and that the system operates reliably and safely.
By meticulously testing and troubleshooting your DIY air compressor, you can identify and address any potential issues before putting the equipment into regular use. This phase is critical for ensuring the functionality, reliability, and safety of your homemade air compressor.
Conclusion
Congratulations! You've successfully navigated the intricate process of building your own DIY air compressor. By understanding the basics of air compressors, gathering the necessary materials and tools, constructing the air tank, installing the compressor pump, connecting the components, adding essential safety features, and conducting thorough testing and troubleshooting, you've embarked on a rewarding journey of craftsmanship and ingenuity.
As you stand back and admire your creation, remember that your DIY air compressor is not just a functional tool – it's a testament to your resourcefulness and determination. Whether you're using it for inflating tires, powering pneumatic tools, or tackling a myriad of DIY projects, your homemade air compressor represents the spirit of self-reliance and the satisfaction of building something with your own hands.
As you continue to explore the world of DIY and home improvement, remember that the skills and knowledge you've gained from this endeavor can be applied to future projects. Whether it's constructing other custom tools, building furniture, or tackling home renovations, the experience of building your DIY air compressor has equipped you with valuable insights and capabilities.
So, take pride in your accomplishment, share your newfound expertise with fellow DIY enthusiasts, and let the hum of your DIY air compressor serve as a reminder of the endless possibilities that unfold when creativity meets craftsmanship. Keep innovating, keep building, and keep embracing the DIY spirit!