Home>Create & Decorate>DIY & Crafts>DIY Guitar Building: How To Create Your Own Custom Instrument
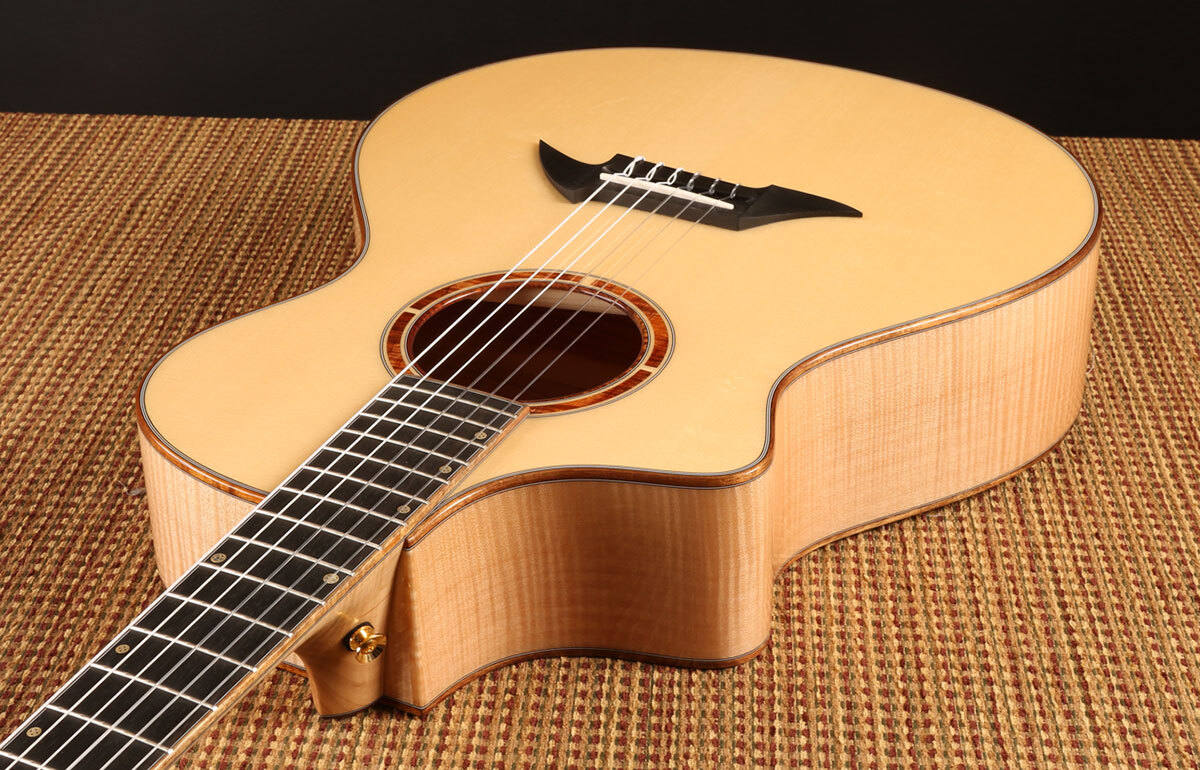
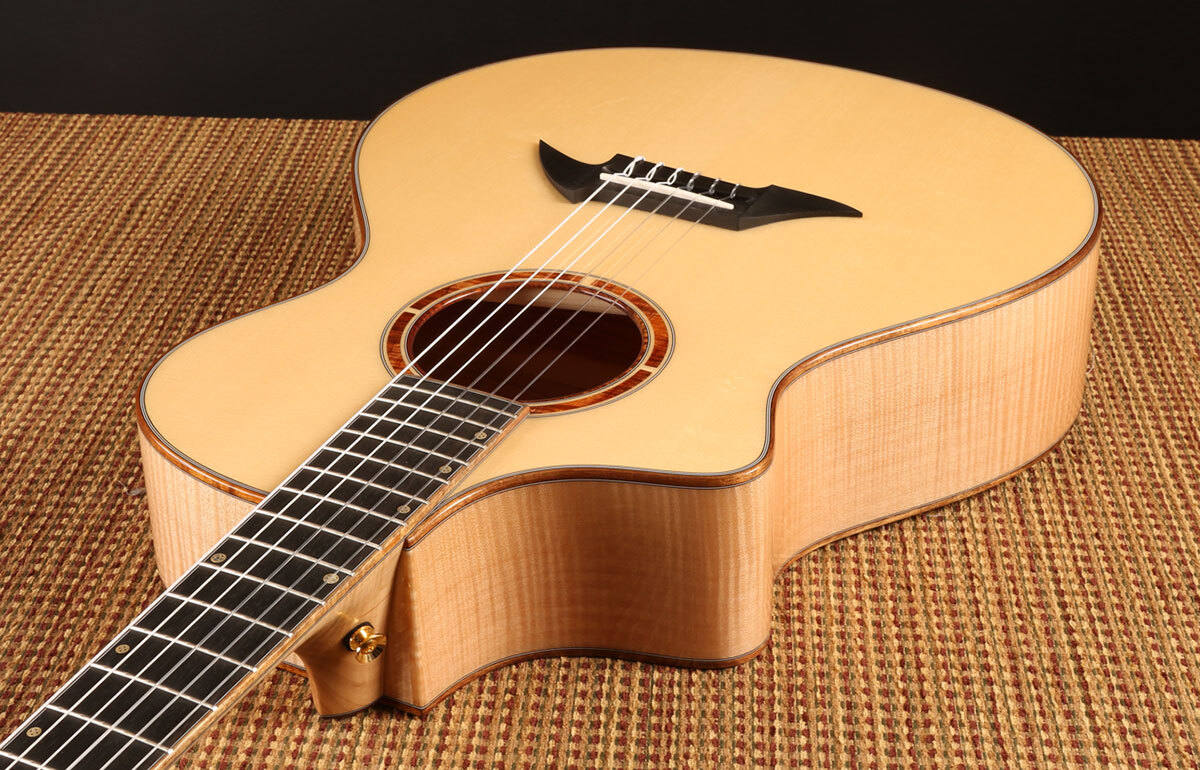
DIY & Crafts
DIY Guitar Building: How To Create Your Own Custom Instrument
Published: June 1, 2024

Senior Editor in Create & Decorate, Kathryn combines traditional craftsmanship with contemporary trends. Her background in textile design and commitment to sustainable crafts inspire both content and community.
Learn how to build your own custom guitar with our DIY guide. Explore step-by-step instructions and expert tips for crafting your dream instrument. Perfect for DIY & Crafts enthusiasts!
(Many of the links in this article redirect to a specific reviewed product. Your purchase of these products through affiliate links helps to generate commission for Twigandthistle.com, at no extra cost. Learn more)
Introduction
So, you've got a passion for music and a love for woodworking, and you've decided to combine the two by building your own custom guitar. Congratulations! Building your own guitar can be a rewarding and fulfilling experience, allowing you to create an instrument that is truly unique to you. Whether you're an experienced woodworker or a novice looking for a new challenge, DIY guitar building is a project that can be both enjoyable and educational. In this guide, we'll walk you through the process of creating your very own custom instrument, from choosing the right materials to putting on the finishing touches. Let's get started!
Read more: How To Build An Acoustic Guitar
Choosing the Right Materials
When it comes to building a custom guitar, selecting the right materials is crucial to the overall sound, feel, and aesthetics of the instrument. Here are the key materials you'll need to consider:
1. Wood
The type of wood you choose for your guitar will have a significant impact on its tone and resonance. Common choices for the body include mahogany, alder, ash, and maple, each offering its own unique characteristics. For the neck, maple and mahogany are popular options due to their stability and tonal qualities.
2. Hardware
Selecting high-quality hardware such as tuning pegs, bridge, and pickups is essential for ensuring your guitar stays in tune, intonates properly, and produces great sound. Consider factors like durability, aesthetics, and compatibility with your chosen wood and design.
3. Electronics
If you're building an electric guitar, choosing the right electronics is crucial. Pickups, potentiometers, and switches all play a role in shaping the guitar's sound. Research different options to find the combination that best suits your musical style and preferences.
Read more: How To Make A Guitar Pedal
4. Finishing Materials
The finish not only protects the wood but also adds to the visual appeal of the guitar. Whether you opt for a natural wood finish or a colored lacquer, selecting the right finishing materials and techniques is essential for achieving the desired look and protection.
By carefully considering and selecting the right materials for your custom guitar, you can ensure that the finished instrument meets your expectations in terms of both aesthetics and performance.
Designing Your Custom Guitar
Designing your custom guitar is where the fun truly begins. This is your chance to let your creativity run wild and bring your vision to life. Here are the key steps to consider when designing your custom guitar:
-
Body Shape: The body shape of a guitar not only affects its aesthetics but also its comfort and playability. Whether you prefer a classic design or something more unconventional, sketch out different body shapes and consider how they will feel when played.
-
Neck Profile: The shape and thickness of the neck can greatly impact how the guitar feels in your hands. Consider different neck profiles and think about how they will complement your playing style.
-
Headstock Design: The headstock is a prominent feature of the guitar and offers an opportunity for personalization. Experiment with different headstock shapes and designs to give your guitar a unique look.
-
Inlays and Bindings: If you're building a guitar with a fretboard, consider the design of the inlays and bindings. These details can add a touch of elegance and individuality to your instrument.
-
Pickguard and Control Layout: For electric guitars, the pickguard and control layout can be customized to suit your preferences. Think about the placement of knobs, switches, and the overall design of the pickguard.
-
Custom Details: Don't be afraid to incorporate custom details that reflect your personality. Whether it's a unique soundhole design, custom truss rod cover, or personalized inlay, these details can make your guitar truly one-of-a-kind.
By taking the time to carefully design your custom guitar, you can ensure that the finished instrument not only looks stunning but also feels and plays exactly the way you want it to. Let your imagination soar and create a guitar that is as unique as you are.
Building the Body and Neck
Building the body and neck of your custom guitar is a pivotal stage in the DIY guitar-building process. It requires precision, attention to detail, and a good understanding of woodworking techniques. Here's a step-by-step guide to help you through this crucial phase:
-
Body Construction:
- Start by selecting the wood for the body and cutting it to the desired shape using a bandsaw or jigsaw.
- Use a router to create the cavities for the electronics and pickups, ensuring they fit snugly and securely.
- Consider the placement of the bridge and tailpiece, and carefully measure and mark their positions before drilling.
-
Neck Crafting:
- Begin by selecting a suitable piece of wood for the neck, ensuring it is straight, stable, and free from defects.
- Use a template to shape the neck profile, then carefully carve it using rasps, files, and sandpaper to achieve the desired contour.
- Install the truss rod and fretboard, ensuring they are aligned and securely attached to the neck.
-
Joining the Body and Neck:
- Once the body and neck are constructed, it's time to join them together.
- Use a precise method such as a mortise and tenon joint or a bolt-on neck joint to securely attach the neck to the body.
-
Fretwork:
- If you're building a guitar with frets, carefully install and level them to ensure a smooth and even playing surface.
- Use a fret crowning file to shape and round the frets, then polish them to a high shine for optimal playability.
-
Final Shaping and Sanding:
- Once the body and neck are joined, it's time for final shaping and sanding.
- Use a combination of hand tools and sanders to smooth out any imperfections and achieve a comfortable, seamless transition between the body and neck.
By following these steps and paying close attention to detail, you can ensure that the body and neck of your custom guitar are crafted to the highest standards, setting the stage for a truly exceptional instrument.
Installing Hardware and Electronics
Installing the hardware and electronics is a crucial step in bringing your custom guitar to life. It involves carefully fitting and positioning the essential components that will determine the instrument's functionality and sound. Here's a detailed guide to help you navigate this stage with precision and confidence:
-
Tuning Pegs and Nut: Begin by installing the tuning pegs onto the headstock. Ensure they are aligned and securely fastened to provide stable tuning. Next, install the nut at the top of the neck, ensuring it is properly seated and spaced to accommodate the strings.
-
Bridge and Tailpiece: For electric guitars, the bridge and tailpiece play a significant role in intonation and string action. Install these components, making sure they are positioned accurately and securely attached to the body. Consider adjusting the bridge height and string spacing to achieve optimal playability.
-
Pickups and Electronics Cavity: If you're building an electric guitar, carefully install the pickups into their designated cavities on the body. Ensure they are positioned at the correct height and angle for balanced output and tonal characteristics. Additionally, install the electronic components such as potentiometers, switches, and input jacks, following the wiring diagram for your specific configuration.
-
Shielding and Grounding: To minimize unwanted noise and interference, consider applying conductive shielding to the electronics cavity and grounding it to the bridge. This can significantly improve the overall performance and clarity of the guitar's electronics.
-
Wiring and Soldering: Take your time to wire the pickups and electronic components according to the schematic diagram. Use high-quality soldering techniques to create secure and reliable connections. Double-check your wiring to ensure everything is properly connected before proceeding.
-
Hardware Alignment and Adjustment: Once all the hardware and electronics are installed, carefully align and adjust each component to ensure proper functionality and playability. This may involve fine-tuning the bridge, adjusting pickup heights, and testing the electronic controls.
By following these steps and paying close attention to detail, you can ensure that the hardware and electronics of your custom guitar are installed with precision and care, setting the stage for a fully functional and great-sounding instrument.
Read more: DIY Cajon: Build Your Own Musical Instrument
Finishing and Assembly
The finishing and assembly stage is where your custom guitar truly comes together, transforming from a collection of parts into a fully functional and visually stunning instrument. This phase requires patience, attention to detail, and a meticulous approach to ensure that every aspect of the guitar meets your expectations. Here's a comprehensive guide to help you navigate the finishing and assembly process with confidence and precision:
-
Sanding and Preparation: Before applying any finish, it's essential to thoroughly sand the body and neck to achieve a smooth and uniform surface. Start with a coarse grit sandpaper to remove any imperfections, then progressively move to finer grits for a silky-smooth finish. Pay close attention to the contours and edges, ensuring they are flawlessly shaped and ready for finishing.
-
Applying the Finish: Whether you prefer a natural wood finish or a colored lacquer, the application process requires careful consideration. Apply the finish in thin, even coats, allowing sufficient drying time between each application. Whether you choose to brush, spray, or wipe on the finish, ensure that the application is uniform and free from drips or runs. Consider experimenting with different techniques such as staining, sunburst finishes, or grain filling to achieve the desired aesthetic.
-
Neck Finishing: When finishing the neck, prioritize a smooth and comfortable feel for optimal playability. Consider using a satin or matte finish for the neck to provide a fast and natural playing surface. Ensure that the finish is applied evenly and does not impede the movement of your hand along the neck.
-
Assembly and Setup: Once the finish has cured, it's time to assemble the various components of the guitar. Install the tuning pegs, nut, bridge, tailpiece, and any remaining hardware with precision and care. String the guitar and carefully adjust the action, intonation, and truss rod to achieve optimal playability and performance. Consider seeking guidance from experienced luthiers or guitar technicians to ensure that the setup is tailored to your playing style and preferences.
-
Final Inspection and Testing: Before considering your custom guitar complete, conduct a thorough inspection of every detail. Check for any imperfections in the finish, ensure that all components are securely fastened, and test the functionality of the electronics and hardware. Play the guitar extensively to assess its playability, tone, and overall feel. Make any necessary adjustments to fine-tune the instrument to your satisfaction.
By following these steps and approaching the finishing and assembly process with meticulous care, you can ensure that your custom guitar is not only visually striking but also a joy to play. Embrace the opportunity to add personal touches and details that make your instrument truly one-of-a-kind, and revel in the satisfaction of bringing your musical vision to life.
Conclusion
In conclusion, building your own custom guitar through the DIY approach is a deeply rewarding and enriching experience. From selecting the finest materials to crafting the body and neck, installing hardware and electronics, and finally, applying the finishing touches, every step of the process allows for personalization and creativity. The end result is not just a musical instrument, but a reflection of your unique style, preferences, and craftsmanship. Whether you're a seasoned woodworker or a passionate musician looking to embark on a new endeavor, the journey of DIY guitar building offers a blend of artistry, technical skill, and the joy of creating something truly exceptional. So, roll up your sleeves, unleash your creativity, and embark on the fulfilling journey of crafting your very own custom guitar.