Home>Create & Decorate>DIY & Crafts>DIY Drone Building: Step-by-Step Guide To Constructing Your Own Drone
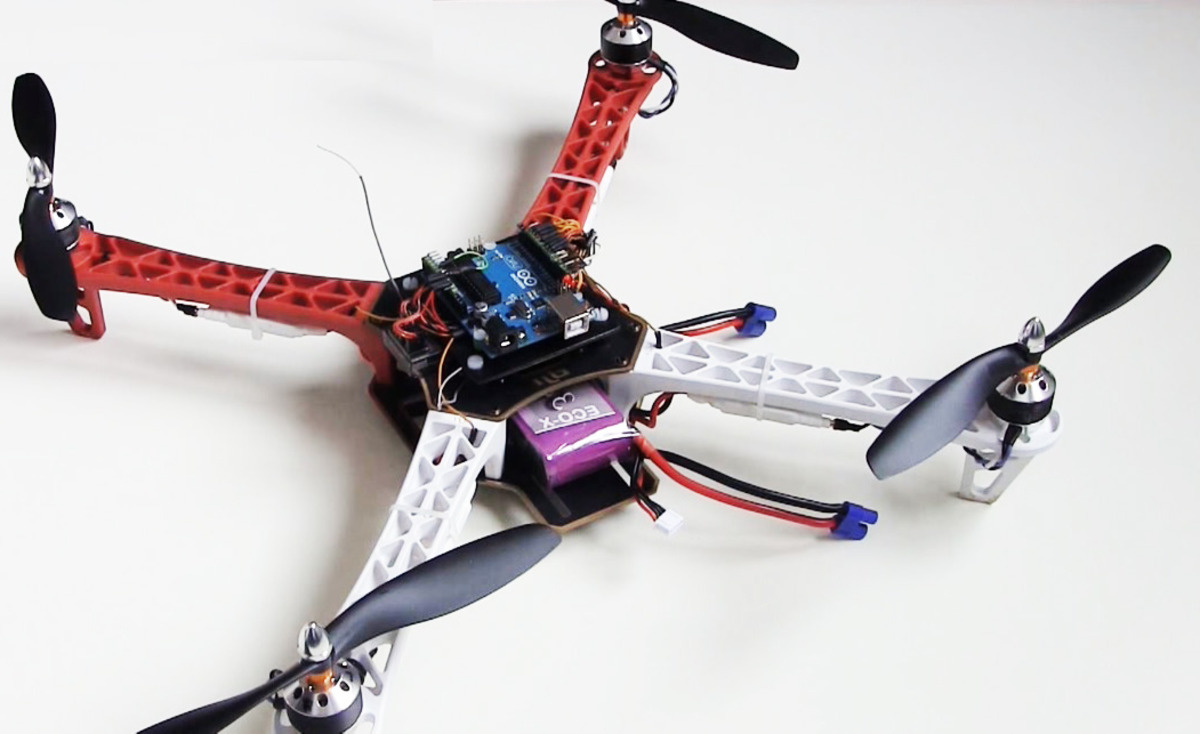
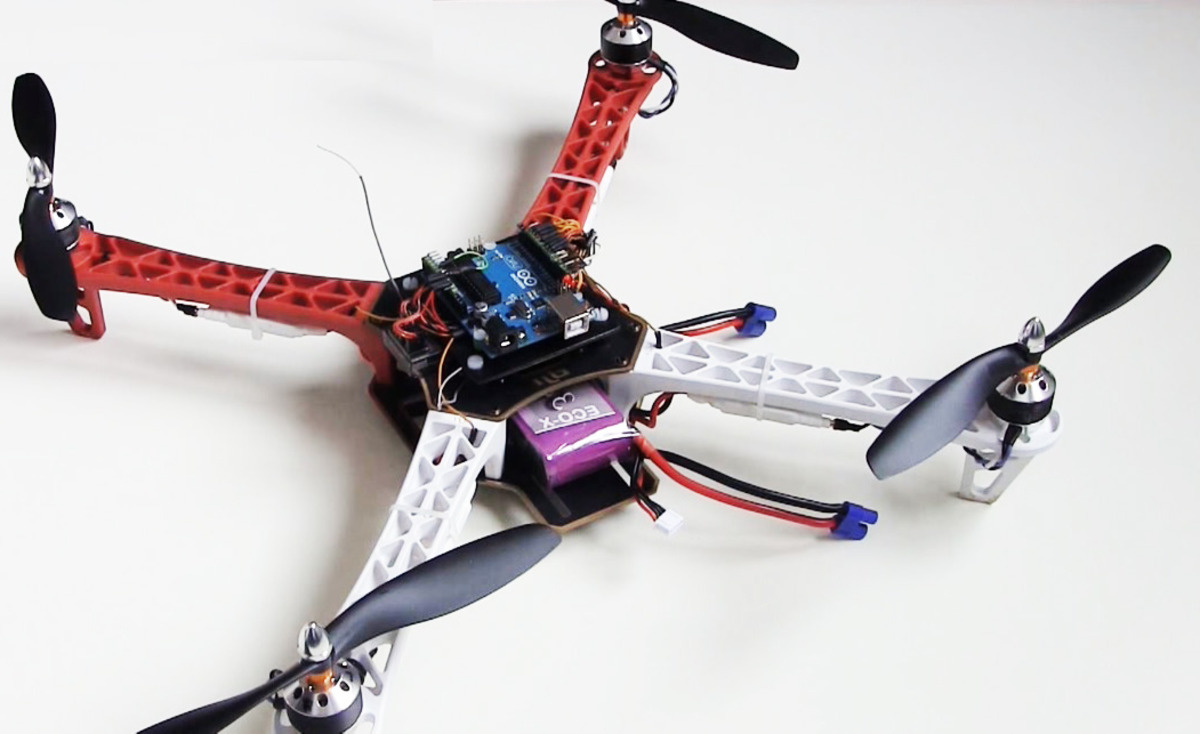
DIY & Crafts
DIY Drone Building: Step-by-Step Guide To Constructing Your Own Drone
Published: February 22, 2024

Content Creator specializing in woodworking and interior transformations. Caegan's guides motivate readers to undertake their own projects, while his custom furniture adds a personal touch.
Learn how to build your own drone with our step-by-step DIY guide. Create a customized drone with our expert tips and instructions. Perfect for DIY & Crafts enthusiasts!
(Many of the links in this article redirect to a specific reviewed product. Your purchase of these products through affiliate links helps to generate commission for Twigandthistle.com, at no extra cost. Learn more)
Introduction
Building your own drone can be an exhilarating and rewarding experience, allowing you to delve into the fascinating world of do-it-yourself (DIY) technology while gaining a deeper understanding of aerial robotics. Whether you're an avid hobbyist, a tech enthusiast, or a professional seeking a customized drone solution, embarking on this journey will not only provide you with a unique aircraft tailored to your specific needs but also equip you with valuable knowledge about drone construction and operation.
As you venture into the realm of DIY drone building, you'll have the opportunity to unleash your creativity and technical prowess, from selecting the components and assembling the intricate parts to fine-tuning the flight performance. By immersing yourself in this hands-on endeavor, you'll gain a profound sense of accomplishment as you witness your creation take flight, soaring through the skies with precision and grace.
Moreover, constructing your own drone offers a deeper level of engagement with the technology, allowing you to grasp the inner workings of each component and how they synergize to achieve controlled flight. This intimate knowledge can be invaluable, especially if you aim to customize your drone for specific applications such as aerial photography, videography, or even drone racing.
Throughout this step-by-step guide, you'll embark on a journey that transcends mere assembly; it's a voyage of discovery, learning, and innovation. Each stage of the process presents an opportunity to hone your skills, troubleshoot challenges, and ultimately witness the culmination of your efforts as your drone takes to the skies under your command.
So, fasten your seatbelt, as we embark on an exhilarating adventure into the realm of DIY drone building. Get ready to unleash your creativity, technical prowess, and passion for flight as we guide you through the intricate process of constructing your very own drone. Let's soar into the world of drone customization and innovation, where the sky is not the limit—it's just the beginning.
Read more: How to Build a DIY Paddle Board Roof Rack
Step 1: Gathering Materials and Tools
Before embarking on the exciting journey of building your own drone, it's essential to gather the necessary materials and tools to ensure a smooth and efficient construction process. Here's a comprehensive list of the components and equipment you'll need to kickstart your DIY drone project:
Materials:
- Drone Frame: Select a durable and lightweight frame that suits your intended use, such as carbon fiber, aluminum, or 3D-printed frames.
- Motors and Propellers: Choose high-quality brushless motors and compatible propellers to provide the necessary thrust and lift for your drone.
- Flight Controller: Opt for a reliable flight controller board equipped with gyroscopes and accelerometers for stable flight performance.
- Electronic Speed Controllers (ESCs): Acquire ESCs that match the specifications of your motors to regulate motor speed and direction.
- Battery: Select a high-capacity lithium polymer (LiPo) battery with the appropriate voltage and discharge rate for your drone's power requirements.
- Power Distribution Board (PDB): Obtain a PDB to distribute power from the battery to the various electronic components of the drone.
- Radio Transmitter and Receiver: Choose a radio control system with a transmitter for piloting the drone and a receiver for communicating with the flight controller.
- Propeller Guards (Optional): If desired, consider adding propeller guards to enhance safety during flight and protect the drone's surroundings.
Tools:
- Soldering Iron and Solder: A quality soldering iron and solder are essential for connecting electrical components and ensuring secure joints.
- Wire Cutters and Strippers: These tools are indispensable for preparing and organizing the wiring harness within the drone.
- Screwdrivers and Allen Keys: Prepare a set of screwdrivers and Allen keys in various sizes to assemble and secure the drone's components.
- Multimeter: A multimeter is crucial for testing electrical connections, voltage, and continuity during the assembly process.
- Adhesives and Fasteners: Keep a supply of adhesives, such as epoxy or hot glue, along with fasteners like zip ties and Velcro straps for securing components.
By meticulously gathering these materials and tools, you'll lay a solid foundation for the construction phase of your DIY drone project. With these essentials at your disposal, you'll be well-equipped to progress to the next exhilarating stage: assembling the frame and bringing your drone to life.
Step 2: Assembling the Frame
Assembling the frame serves as the foundational step in constructing your own drone. The frame not only provides structural support but also determines the overall stability and maneuverability of the drone. Here's a detailed guide on how to expertly assemble the frame of your DIY drone:
-
Frame Selection: Begin by carefully selecting a drone frame that aligns with your specific requirements. Consider factors such as material, size, and design. Carbon fiber frames are renowned for their lightweight yet robust nature, making them a popular choice among DIY drone builders. Alternatively, aluminum frames offer durability and are well-suited for heavy-lift applications. If you're inclined towards customization, 3D-printed frames provide flexibility in design and material composition.
-
Component Layout: Lay out the frame components in an organized manner, ensuring that all necessary parts are readily accessible. This includes the main frame plates, arms, and associated hardware such as screws and standoffs. Familiarize yourself with the frame's configuration and the intended placement of electronic components, as this will guide the assembly process.
-
Arm Attachment: Securely attach the arms to the main frame plates using the designated mounting points and hardware. Pay close attention to the orientation and alignment of the arms to maintain symmetry and balance. Utilize a torque wrench or screwdriver to achieve the recommended fastening torque, ensuring that the arms are firmly affixed to the frame.
-
Integration of Components: As you progress, consider the integration of additional components such as the power distribution board (PDB) and electronic speed controllers (ESCs) within the frame structure. Strategically position these elements to optimize weight distribution and maintain a streamlined layout for the subsequent installation of motors and other electronic modules.
-
Secure Fastening: Double-check the fastening of all components to mitigate the risk of loosening during flight. Utilize thread-locking compounds on critical fasteners to prevent unintended loosening due to vibration and operational stresses. This meticulous approach to fastening ensures the structural integrity of the frame, promoting a safe and reliable flight experience.
By meticulously following these steps, you'll successfully assemble the frame of your DIY drone, laying the groundwork for the integration of propulsion systems and electronic components. The frame serves as the backbone of your aerial platform, providing the necessary support and structural integrity for the seamless operation of your custom-built drone. With the frame assembly completed, you're now poised to progress to the next stage of this exhilarating journey: attaching motors and propellers to bring your drone one step closer to flight-ready status.
Read more: How to Build a DIY Sauna Door
Step 3: Attaching Motors and Propellers
Attaching motors and propellers is a critical phase in the construction of your DIY drone, as it directly influences the propulsion and maneuvering capabilities of the aircraft. This step demands precision and attention to detail to ensure optimal performance and stability during flight. Here's a comprehensive guide on how to expertly attach motors and propellers to your drone:
-
Motor Selection: Begin by selecting high-quality brushless motors that align with your drone's specifications and intended use. Consider factors such as thrust-to-weight ratio, motor size, and compatibility with the frame and propellers. Opt for motors that offer a balance between power output and energy efficiency, catering to the unique requirements of your drone.
-
Mounting Motors: Carefully mount the selected motors onto the designated motor mounts or arms of the drone frame. Ensure that the motor orientation corresponds to the specific configuration required for your drone's flight dynamics. Secure the motors using the provided mounting screws, adhering to the recommended torque specifications to prevent loosening during operation.
-
Propeller Installation: Select propellers that complement the thrust characteristics of the chosen motors, considering factors such as diameter, pitch, and material composition. Carefully attach the propellers to the motor shafts, ensuring that they are securely fastened and balanced to minimize vibration and enhance efficiency. Pay attention to the propeller rotation direction, adhering to the designated "clockwise" and "counterclockwise" configurations to facilitate stable flight.
-
Balancing Propellers: Prior to finalizing the propeller installation, it's essential to balance the propellers to mitigate vibration and optimize performance. Utilize a propeller balancer or dynamic balancing techniques to identify and rectify any imbalance in the propeller blades. This meticulous process contributes to smoother operation and reduces stress on the motors and airframe during flight.
-
Motor Wiring: Organize the motor wiring harness, ensuring that the motor leads are neatly routed and secured to prevent entanglement or interference with other components. Employ cable management techniques such as heat shrink tubing and cable ties to maintain a tidy and reliable electrical connection.
By meticulously following these steps, you'll expertly attach motors and propellers to your DIY drone, setting the stage for the integration of the flight controller and electronic speed controllers (ESCs). This pivotal phase brings your drone one step closer to achieving flight-ready status, as the propulsion system forms the cornerstone of its aerial capabilities. With motors and propellers securely in place, your custom-built drone is poised to soar through the skies with precision and agility, embodying the culmination of your craftsmanship and technical expertise.
Step 4: Installing the Flight Controller
Installing the flight controller is a pivotal stage in the construction of your DIY drone, as it serves as the central nervous system that governs the aircraft's stability, orientation, and flight dynamics. The flight controller, equipped with gyroscopes and accelerometers, plays a crucial role in stabilizing the drone during flight, compensating for external forces and maintaining a steady aerial posture. Here's a detailed exploration of the process involved in installing the flight controller to elevate your drone-building endeavor to new heights.
Selection of Flight Controller
Begin by selecting a reliable and feature-rich flight controller that aligns with your specific requirements and operational preferences. Consider factors such as sensor precision, compatibility with your chosen frame and propulsion system, as well as the availability of advanced flight modes and programmable parameters. Popular options include the Betaflight, Pixhawk, and Ardupilot flight controllers, each offering a diverse range of capabilities tailored to various drone applications.
Mounting and Orientation
Carefully mount the flight controller onto the designated location within the drone frame, ensuring that it is securely affixed and insulated from vibration and external disturbances. Pay meticulous attention to the orientation of the flight controller, aligning it with the aircraft's primary axis to facilitate accurate sensor readings and responsive control inputs. Utilize vibration-damping mounting solutions, such as rubber standoffs or silicone grommets, to minimize the impact of motor and propeller-induced vibrations on the flight controller's performance.
Read more: How to Build a DIY Pivot Door
Wiring and Connectivity
Establish the necessary wiring connections between the flight controller and other essential components, including electronic speed controllers (ESCs), receiver, and power distribution board (PDB). Adhere to the prescribed wiring diagrams and pin configurations provided by the flight controller manufacturer, ensuring that each connection is secure and free from potential short circuits or signal interference. Employ cable management techniques to organize the wiring harness, mitigating the risk of entanglement and simplifying troubleshooting and maintenance tasks in the future.
Firmware Configuration
Upon physical installation, proceed to configure the firmware and parameters of the flight controller using dedicated software interfaces such as Betaflight Configurator or Mission Planner. Calibrate the accelerometer and gyroscopes to ensure accurate sensor readings, and customize flight modes, control rates, and stabilization settings to suit your piloting preferences. Thoroughly test the responsiveness of the flight controller inputs and verify the correct orientation and behavior of the aircraft through the software interface before proceeding to the next phase of the drone construction process.
By meticulously executing the installation of the flight controller, you'll establish a robust foundation for the precise control and stability of your DIY drone. The flight controller's seamless integration into the aircraft's architecture marks a significant milestone in the construction journey, bringing your custom-built drone one step closer to achieving flight-ready status. With the flight controller poised to orchestrate the aerial symphony, your drone embodies the fusion of cutting-edge technology and your unwavering passion for innovation and exploration.
Step 5: Connecting Electronic Speed Controllers (ESCs)
Connecting electronic speed controllers (ESCs) is a pivotal phase in the construction of your DIY drone, as these components play a crucial role in regulating the speed and direction of the motors, thereby influencing the aircraft's maneuverability and responsiveness. This step demands meticulous attention to detail and precision to ensure seamless integration and optimal performance of the propulsion system. Here's a comprehensive exploration of the process involved in connecting electronic speed controllers (ESCs) to elevate your drone-building endeavor to new heights.
ESC Selection and Placement
Begin by selecting high-quality electronic speed controllers (ESCs) that align with the specifications of your chosen motors and the overall power requirements of your drone. Consider factors such as current rating, voltage compatibility, and programmable features to cater to your specific flight preferences. Once selected, carefully position the ESCs within the drone frame, ensuring that they are strategically located to minimize wiring complexity and maintain a balanced weight distribution.
Read more: How to Build DIY Roof Scaffolding
Motor and Power Distribution Board (PDB) Connections
Establish the necessary wiring connections between the ESCs and the respective motors, adhering to the prescribed motor-ESC pairing to ensure correct motor rotation direction and synchronization. Pay meticulous attention to the soldering or connector-based connections, ensuring that each joint is secure and free from potential electrical faults. Additionally, connect the ESCs to the power distribution board (PDB) to receive the necessary power supply from the drone's battery, adhering to the designated positive and negative terminals to prevent polarity-related issues.
Calibration and Testing
Upon completing the ESC-motor and ESC-PDB connections, proceed to calibrate the electronic speed controllers to synchronize throttle response and ensure uniform motor operation. Utilize dedicated calibration procedures provided by the ESC manufacturer, which typically involve configuring throttle endpoints and calibrating the motor control range to align with the radio transmitter's input signals. Thoroughly test each motor's response to throttle inputs, verifying smooth acceleration and deceleration without any irregular behavior or synchronization issues.
Cable Management and Insulation
Organize the ESC wiring harness within the drone frame, employing cable management techniques such as heat shrink tubing, cable ties, and routing channels to maintain a tidy and secure wiring layout. Insulate the ESCs and associated wiring from potential sources of electrical interference and mechanical abrasion, safeguarding the integrity of the connections and promoting long-term reliability during flight operations.
By meticulously executing the process of connecting electronic speed controllers (ESCs), you'll establish a robust foundation for the precise control and propulsion of your DIY drone. The seamless integration of ESCs into the aircraft's architecture marks a significant milestone in the construction journey, bringing your custom-built drone one step closer to achieving flight-ready status. With the ESCs poised to regulate the aerial dynamics, your drone embodies the fusion of cutting-edge technology and your unwavering passion for innovation and exploration.
Step 6: Mounting the Battery and Power Distribution Board
Mounting the battery and power distribution board (PDB) is a crucial phase in the construction of your DIY drone, as it establishes the core power supply and distribution system essential for the aircraft's operation. This step demands meticulous attention to detail and precision to ensure the secure integration and reliable performance of the electrical components. Here's a comprehensive exploration of the process involved in mounting the battery and power distribution board to elevate your drone-building endeavor to new heights.
Read more: How to Build a DIY Safe Door
Battery Selection and Placement
Begin by selecting a high-capacity lithium polymer (LiPo) battery that aligns with the voltage and current requirements of your drone's propulsion system. Consider factors such as capacity, discharge rate, and physical dimensions to ensure compatibility with the chosen frame and electronic components. Once selected, carefully position the battery within the designated battery compartment or mounting area of the drone frame, ensuring that it is securely fastened and insulated from potential sources of mechanical stress or vibration.
Power Distribution Board Integration
Install the power distribution board (PDB) within the drone frame, positioning it in close proximity to the battery and electronic speed controllers (ESCs) to minimize wiring complexity and optimize power delivery efficiency. Securely fasten the PDB to the frame using the provided mounting hardware, ensuring that it is insulated from direct contact with conductive surfaces and potential sources of electrical interference. Verify that the PDB's positive and negative terminals align with the corresponding connections from the battery and ESCs, facilitating a streamlined power distribution network.
Wiring and Connection Management
Establish the necessary wiring connections between the battery, power distribution board, and electronic speed controllers, adhering to the prescribed polarity and current-carrying capacity to prevent electrical faults or power surges. Employ cable management techniques such as braided sleeves, insulated wire connectors, and strain relief mechanisms to organize the wiring harness and mitigate the risk of entanglement or chafing during flight operations. Verify the integrity of each electrical connection and perform continuity tests to ensure a reliable power distribution network.
Safety Considerations and Precautions
Prioritize safety measures by implementing fail-safe mechanisms such as voltage alarms, current sensors, and thermal protection devices to monitor the battery's status and prevent over-discharge or overloading conditions. Insulate the battery and power distribution board from potential sources of mechanical impact or environmental hazards, safeguarding the electrical components from damage and ensuring the overall reliability of the power supply system.
By meticulously executing the process of mounting the battery and power distribution board, you'll establish a robust foundation for the reliable power supply and distribution of your DIY drone. The seamless integration of the battery and PDB into the aircraft's architecture marks a significant milestone in the construction journey, bringing your custom-built drone one step closer to achieving flight-ready status. With the power supply system poised to energize the aerial symphony, your drone embodies the fusion of cutting-edge technology and your unwavering passion for innovation and exploration.
Step 7: Adding the Radio Transmitter and Receiver
Adding the radio transmitter and receiver to your DIY drone is a pivotal step that establishes the vital communication link between the pilot and the aircraft, enabling precise control and seamless maneuvering during flight operations. This phase demands meticulous attention to detail and precision to ensure the seamless integration and reliable performance of the radio control system. Here's a comprehensive exploration of the process involved in adding the radio transmitter and receiver to elevate your drone-building endeavor to new heights.
Transmitter Selection and Configuration
Begin by selecting a high-quality radio transmitter that aligns with your piloting preferences and the operational requirements of your drone. Consider factors such as the number of channels, transmission range, and ergonomic design to ensure a comfortable and intuitive piloting experience. Familiarize yourself with the transmitter's control layout and programmable features, customizing control inputs, and flight modes to suit your specific piloting style and the intended applications of the drone.
Receiver Installation and Binding
Carefully install the radio receiver within the drone's frame, positioning it in a secure and accessible location to facilitate reliable signal reception and minimize electromagnetic interference. Follow the manufacturer's guidelines to bind the receiver with the transmitter, establishing a secure and encrypted communication link to prevent signal conflicts and unauthorized control access. Verify the receiver's signal strength and responsiveness through pre-flight checks, ensuring that it exhibits consistent and reliable reception of control inputs from the transmitter.
Antenna Placement and Orientation
Strategically position the receiver's antennas within the drone frame, orienting them to optimize signal reception and minimize signal attenuation during flight maneuvers. Utilize antenna extension cables or mounting brackets to position the antennas away from potential sources of electromagnetic interference, such as power distribution components and high-current wiring harnesses. Perform range tests and signal quality assessments to validate the effectiveness of the antenna placement and optimize the radio link's reliability and responsiveness.
Read more: How to Build a DIY Kayak Roof Rack
Fail-Safe Programming and Testing
Implement fail-safe programming on the radio transmitter and receiver, configuring automatic control response protocols in the event of signal loss or transmitter malfunction. Define fail-safe behaviors such as throttle cut-off or return-to-home modes to ensure the safe and controlled recovery of the drone in unforeseen circumstances. Thoroughly test the fail-safe functionalities through ground-based simulations and controlled flight scenarios, verifying the system's responsiveness and reliability in mitigating potential flight hazards.
By meticulously executing the process of adding the radio transmitter and receiver, you'll establish a robust foundation for the precise control and communication of your DIY drone. The seamless integration of the radio control system into the aircraft's architecture marks a significant milestone in the construction journey, bringing your custom-built drone one step closer to achieving flight-ready status. With the radio transmitter and receiver poised to orchestrate the aerial symphony, your drone embodies the fusion of cutting-edge technology and your unwavering passion for innovation and exploration.
Step 8: Testing and Calibrating the Drone
The final step in the exhilarating journey of DIY drone building involves comprehensive testing and precise calibration to ensure the optimal performance and safety of the aircraft. This critical phase serves as the ultimate validation of your meticulous construction efforts, allowing you to fine-tune the drone's systems and verify its readiness for flight operations.
Pre-Flight Checks
Before initiating the testing phase, conduct thorough pre-flight checks to scrutinize the integrity of the drone's components and systems. Inspect the structural integrity of the frame, ensuring that all fasteners, motor mounts, and electronic modules are securely affixed. Verify the functionality of the propulsion system by conducting motor spin tests, confirming the correct rotation direction and smooth operation of each motor. Additionally, scrutinize the wiring harness for any signs of damage, abrasion, or loose connections, rectifying any identified issues to uphold the electrical integrity of the drone.
Flight Controller Calibration
Initiate the calibration of the flight controller by verifying the accuracy of sensor readings and control inputs. Utilize dedicated software interfaces to calibrate the accelerometer, gyroscope, and magnetometer, ensuring precise orientation detection and stabilization capabilities. Fine-tune the control response rates and stabilization parameters to align with your piloting preferences, optimizing the drone's responsiveness and maneuvering characteristics.
Read more: How to Build a Metal Door
Propulsion System Testing
Conduct comprehensive propulsion system tests to validate the synchronization and responsiveness of the motors and electronic speed controllers (ESCs). Ascertain uniform throttle response across all motors, confirming smooth acceleration and deceleration without any irregular behavior or synchronization issues. Verify the correct operation of the propellers, ensuring balanced thrust output and minimal vibration during motor spin-up and spin-down sequences.
Radio Control Verification
Initiate ground-based radio control verification tests to validate the responsiveness and range of the transmitter-receiver link. Execute control input checks to ensure accurate and immediate response from the drone's control surfaces, confirming the absence of signal latency or interference. Perform range tests to assess the transmitter's effective communication range and signal robustness, ensuring reliable control connectivity throughout the designated flight envelope.
Flight Simulation and Stability Assessment
Conduct controlled flight simulations in a safe and open environment to assess the drone's stability, maneuverability, and overall flight characteristics. Execute gradual ascent and descent maneuvers, verifying the aircraft's response to altitude changes and throttle adjustments. Evaluate the drone's roll, pitch, and yaw stability through coordinated control inputs, ensuring precise and predictable flight behavior. Additionally, assess the effectiveness of the flight controller's stabilization and auto-leveling features, validating its capacity to maintain a steady and level flight posture.
Safety and Emergency Procedures
Establish comprehensive safety and emergency procedures to mitigate potential flight hazards and ensure the safe operation of the drone. Define fail-safe behaviors such as automatic return-to-home modes, low battery voltage warnings, and motor cut-off protocols to safeguard against unforeseen contingencies. Verify the effectiveness of these safety measures through controlled simulations, validating their capacity to avert potential flight hazards and facilitate the safe recovery of the drone in adverse conditions.
By meticulously executing the testing and calibration phase, you'll ascertain the airworthiness and operational readiness of your DIY drone, culminating in the realization of your construction endeavor. The comprehensive validation of the drone's systems and performance instills confidence in its capabilities, setting the stage for exhilarating flight experiences and the exploration of aerial vistas. With the meticulous testing and calibration process completed, your custom-built drone stands as a testament to your technical prowess, innovation, and unwavering passion for the art of flight.
Read more: How to Build a DIY Hutch
Conclusion
In conclusion, the journey of DIY drone building transcends mere assembly; it's a voyage of discovery, learning, and innovation. Each stage of the process presents an opportunity to hone skills, troubleshoot challenges, and ultimately witness the culmination of efforts as the drone takes to the skies under the builder's command.
The process begins with gathering materials and tools, a crucial step that sets the foundation for the entire construction endeavor. From selecting the frame and propulsion components to acquiring the necessary tools for assembly, meticulous planning and preparation are essential to ensure a smooth and efficient build.
Assembling the frame and attaching motors and propellers form the structural and propulsion backbone of the drone. These stages demand precision and attention to detail, as the frame provides structural support and determines the aircraft's stability, while the motors and propellers dictate its maneuverability and flight performance.
The installation of the flight controller and the connection of electronic speed controllers (ESCs) further enhance the drone's capabilities, enabling precise control, stabilization, and power regulation. These components serve as the central nervous system and power distribution network, respectively, ensuring the seamless orchestration of the aircraft's aerial symphony.
Adding the radio transmitter and receiver establishes the vital communication link between the pilot and the drone, enabling precise control and seamless maneuvering during flight operations. This phase marks the culmination of the drone's physical construction, setting the stage for comprehensive testing and calibration.
The final step involves comprehensive testing and precise calibration to ensure the optimal performance and safety of the aircraft. Thorough pre-flight checks, flight controller calibration, propulsion system testing, radio control verification, and flight simulation and stability assessment collectively validate the airworthiness and operational readiness of the DIY drone.
Throughout this journey, the builder gains a profound sense of accomplishment and a deeper understanding of aerial robotics. The hands-on experience not only fosters technical expertise but also ignites a passion for innovation and exploration. As the drone takes flight, it embodies the fusion of cutting-edge technology and unwavering dedication, soaring as a testament to the builder's creativity and ingenuity.
In essence, DIY drone building is not just about constructing an aircraft; it's about embarking on an exhilarating adventure, unleashing creativity, and pushing the boundaries of what is possible. It's a testament to the human spirit of exploration and innovation, where the sky is not the limit—it's just the beginning.