Home>Home & Furniture>Garage & Basement>How to Build a DIY Garage Gantry Crane
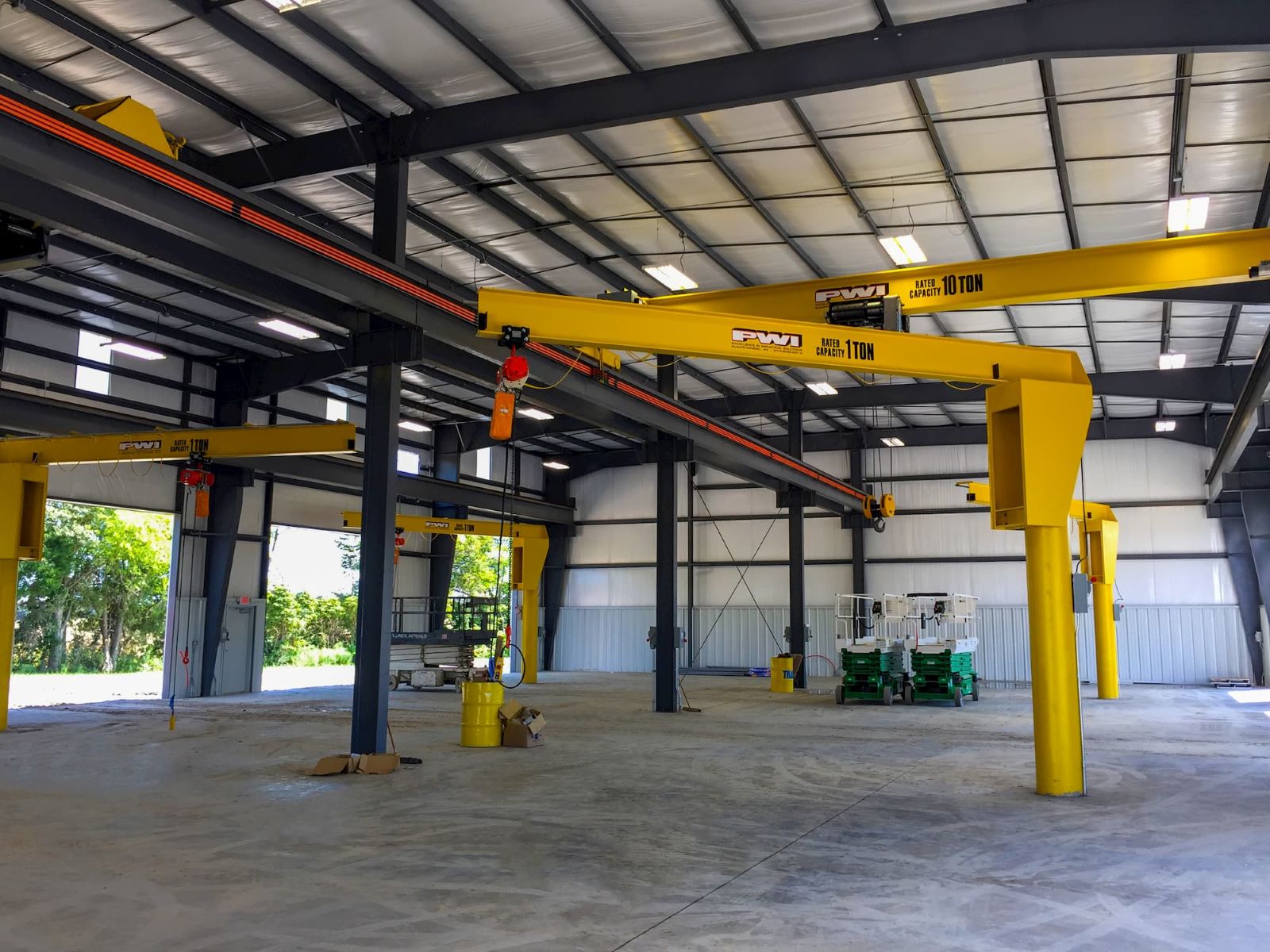
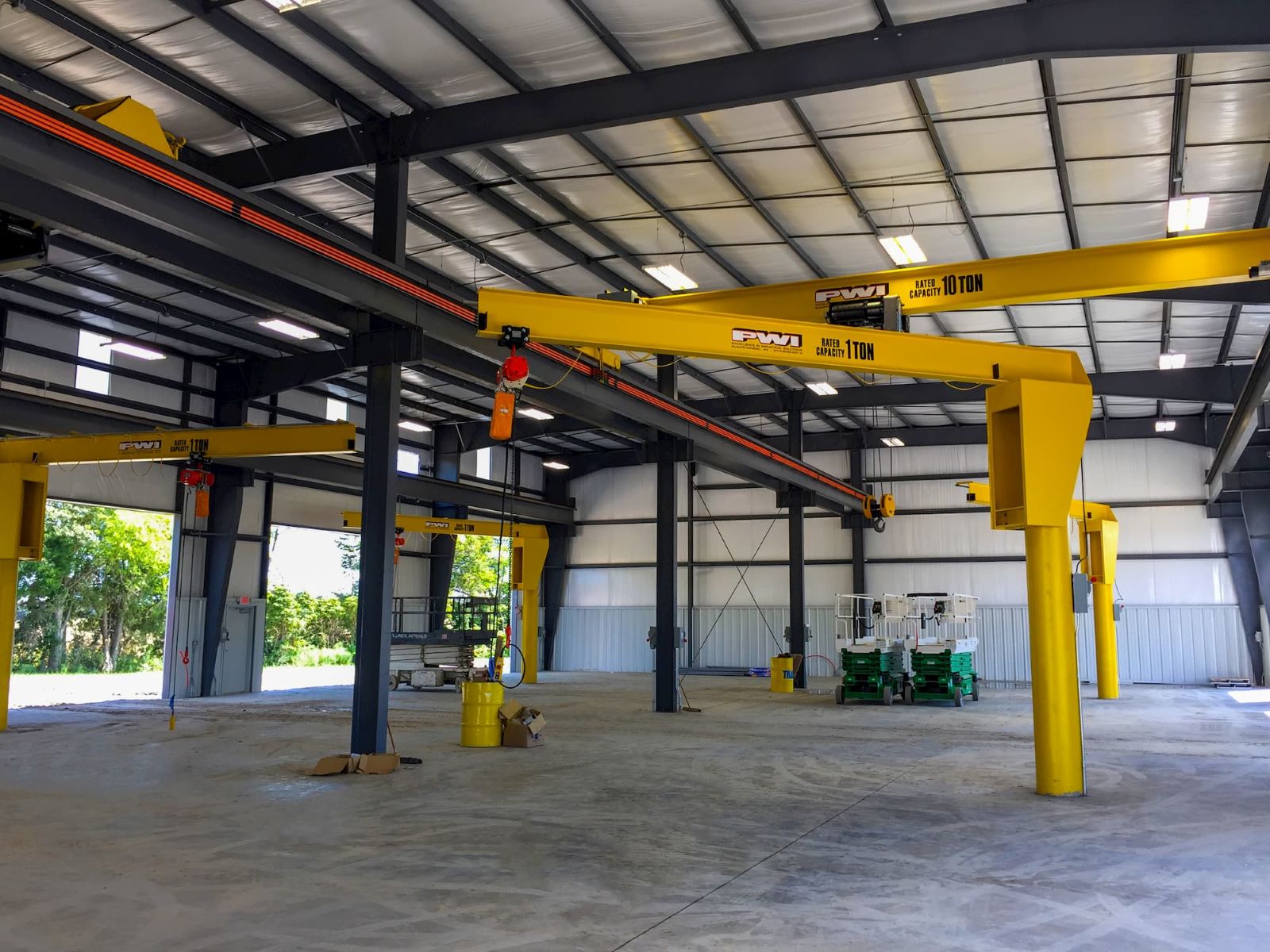
Garage & Basement
How to Build a DIY Garage Gantry Crane
Published: September 24, 2024
Learn how to build a DIY garage gantry crane with our step-by-step guide. Perfect for lifting heavy objects safely and efficiently in your garage or workshop.
(Many of the links in this article redirect to a specific reviewed product. Your purchase of these products through affiliate links helps to generate commission for Twigandthistle.com, at no extra cost. Learn more)
Building a DIY garage gantry crane can save you money and provide a practical solution for lifting heavy items. This project involves basic materials and tools, making it accessible for those with some DIY experience. You’ll need metal or wood beams, a hoist, and casters for mobility. A gantry crane helps with tasks like moving engines, heavy tools, or bulky equipment in your garage. Understanding the steps and safety measures will ensure a sturdy and reliable crane. Let’s dive into the materials, tools, and steps required to build your own garage gantry crane.
Preparation Steps
Gather Materials: Collect steel beams, bolts, nuts, washers, casters, and a hoist. Ensure all materials are rated for the weight you plan to lift.
Safety Gear: Wear safety goggles, gloves, and steel-toed boots. Use a hard hat if working under suspended loads.
Workspace Setup: Clear the garage floor. Ensure there’s enough space to move around. Lay down a tarp to catch debris.
Measure and Mark: Measure the height and width needed for the crane. Mark the steel beams where cuts and holes will go.
Cutting and Drilling: Use a metal saw to cut beams to size. Drill holes for bolts. Ensure cuts and holes are precise.
Assemble Frame: Bolt the vertical beams to the horizontal beam. Tighten all bolts securely.
Attach Casters: Bolt casters to the bottom of the vertical beams. Ensure they are rated for the crane’s load.
Install Hoist: Attach the hoist to the horizontal beam. Follow the manufacturer’s instructions for secure attachment.
Test Stability: Before lifting heavy objects, test the crane with lighter loads. Check for any wobbling or instability.
Final Safety Check: Inspect all bolts, casters, and the hoist. Ensure everything is secure and functioning properly.
Materials and Tools Needed
Materials Needed:
- Steel Beams: These will form the main structure. Choose strong, durable steel for safety.
- Steel Plates: Used for connecting beams and adding stability.
- Bolts and Nuts: Essential for securing steel parts together.
- Casters: Heavy-duty wheels to make the crane mobile.
- Hoist: The lifting mechanism. Choose one with the appropriate weight capacity.
- Paint: To protect steel from rust and corrosion.
Tools Needed:
- Welding Machine: For joining steel parts securely.
- Drill: To make holes for bolts.
- Wrenches: For tightening bolts and nuts.
- Measuring Tape: Ensures accurate measurements.
- Level: To make sure everything is straight and balanced.
- Safety Gear: Includes gloves, goggles, and a welding helmet for protection.
Skill Level and Time Required
Skill Level: Advanced
Estimated Time Required: 2-3 days
- Planning and Design: 4-6 hours
- Gathering Materials: 2-3 hours
- Cutting and Preparing Metal: 6-8 hours
- Welding and Assembly: 8-10 hours
- Painting and Finishing: 4-6 hours
- Testing and Adjustments: 2-3 hours
Step-by-Step Instructions
Gather Materials:
- Steel or aluminum beams
- Four heavy-duty casters
- Bolts, nuts, and washers
- Metal cutting saw
- Drill and bits
- Measuring tape
- Wrenches
- Welding machine (if welding)
Measure and Cut Beams:
- Measure the height and width needed for your garage.
- Cut two vertical beams for the sides.
- Cut one horizontal beam for the top.
Drill Holes:
- Drill holes at the top of the vertical beams for attaching the horizontal beam.
- Drill holes at the bottom of the vertical beams for attaching the casters.
Assemble the Frame:
- Attach the horizontal beam to the top of the vertical beams using bolts, nuts, and washers.
- Ensure the frame is square and level.
Attach Casters:
- Bolt the casters to the bottom of the vertical beams.
- Ensure they swivel and roll smoothly.
Reinforce Joints:
- Add diagonal braces between the vertical and horizontal beams for extra stability.
- Use bolts or weld the braces in place.
Install Hoist:
- Attach a hoist or pulley system to the horizontal beam.
- Ensure it can move freely along the beam.
Test the Crane:
- Check all bolts and joints for tightness.
- Test the crane with a light load to ensure stability and functionality.
Paint and Finish:
- Paint the crane to prevent rust.
- Add any additional safety features like locks or stops.
Helpful Tips and Tricks
Measure twice, cut once. Always double-check measurements before cutting materials. This saves time and prevents waste.
Use quality materials. Opt for strong, durable materials like steel or heavy-duty wood. This ensures the crane can handle heavy loads safely.
Pre-drill holes. Pre-drilling prevents wood from splitting and makes assembly easier.
Level the base. Ensure the base is level before assembling the crane. This keeps the structure stable and safe.
Lubricate moving parts. Apply grease or oil to pulleys and wheels. This reduces friction and extends the life of the crane.
Label parts. Labeling helps keep track of components, making assembly quicker and more organized.
Common mistakes to avoid:
Overloading the crane. Exceeding weight limits can cause the crane to fail. Always check the maximum load capacity.
Ignoring safety gear. Wear gloves, safety glasses, and sturdy footwear. This protects you from injuries.
Skipping the manual. Follow instructions carefully. Skipping steps can lead to structural issues.
Alternatives for materials or methods:
Use aluminum. Aluminum is lighter than steel but still strong. This makes the crane easier to move.
Opt for casters with brakes. Braked casters keep the crane stationary when needed, adding an extra layer of safety.
Consider a chain hoist. A chain hoist can be more durable than a rope hoist, especially for heavier loads.
Estimating the Cost
Steel Beams: $150-$300 depending on size and quality.
Welding Machine: $200-$500. Renting costs around $50/day.
Welding Rods: $20 for a pack.
Cutting Tools: $50-$100. An angle grinder is a good option.
Bolts and Nuts: $30-$50. Ensure they are heavy-duty.
Casters/Wheels: $40-$80. Heavy-duty ones are necessary.
Paint: $20-$40. Protects against rust.
Safety Gear: $50-$100. Includes gloves, goggles, and a welding helmet.
Hoist: $100-$200. Manual or electric options available.
Total Cost: $660-$1,440.
Budget-Friendly Alternatives:
- Borrow or rent a welding machine.
- Use second-hand steel beams.
- Opt for manual hoist instead of electric.
Possible Variations and Customizations
Materials: Instead of using steel beams, consider wood for a lighter, easier-to-handle structure. Aluminum can also be a good choice for a rust-resistant frame.
Colors: Paint the crane in bright colors like yellow or orange for better visibility. Use black or gray for a more industrial look.
Styles: Add adjustable legs for uneven floors. Install swivel casters for easier movement. Attach hooks or shelves for tool storage.
Lifting Mechanism: Swap the manual hoist for an electric hoist to lift heavier loads with less effort. Use a chain hoist for more control over lifting speed.
Safety Features: Add safety locks to prevent accidental lowering. Install warning lights or alarms to signal when the crane is in use.
Customization: Personalize the crane with decals or stickers. Add padding to the beams to protect items being lifted.
Eco-Friendly Building Tips
Reusing old metal pipes can be a great way to build the frame. Look for scrap metal at local junkyards or recycling centers. Wooden beams from old construction projects can also be repurposed for the base. Use eco-friendly paint or sealant to protect the wood and metal from rust and wear.
For the lifting mechanism, consider using a second-hand chain hoist. Many times, these can be found at garage sales or online marketplaces. Recycled rubber can be used for the wheels to make them durable and eco-friendly.
When assembling, opt for bolts and screws made from recycled materials. This reduces the need for new metal production. Lastly, ensure all materials are non-toxic and safe for the environment.
Your DIY Gantry Crane Awaits
Building a DIY garage gantry crane isn't just a fun project; it's a game-changer for your workspace. You've learned how to gather materials, follow steps, and ensure safety. Now, you can lift heavy stuff with ease, making your garage more efficient. Remember, always double-check your work and use quality materials. This crane will save you time and effort, letting you focus on other projects. So, roll up your sleeves and get started. Your new gantry crane is just a few steps away. Happy building!
What materials do I need to build a DIY garage gantry crane?
You'll need steel beams, casters, bolts, nuts, washers, and a hoist. Make sure to get a welding machine and safety gear too.
How much weight can a DIY gantry crane lift?
It depends on the materials and design. Typically, a well-built DIY crane can lift between 500 to 2000 pounds. Always check the specs of your materials.
Do I need any special tools?
Yes, you'll need a welding machine, drill, wrenches, and a measuring tape. A level and safety gear like gloves and goggles are also important.
How long does it take to build one?
It usually takes a weekend if you have all the materials and tools ready. Plan for about 10-15 hours of work.
Is it safe to build my own gantry crane?
Yes, if you follow safety guidelines and use quality materials. Make sure to double-check all connections and test the crane with a lighter load first.
Can I move the gantry crane around my garage?
Absolutely! Adding casters to the base allows you to roll the crane to different spots. Just make sure the floor is smooth and level.
Do I need any permits to build a gantry crane?
Usually, you don't need a permit for a DIY project in your garage. However, it's a good idea to check local regulations just to be sure.